Warehouse case picking is a foundational operation in logistics and supply chain. Case picking methods have evolved, adapting to the demands of growing global trade, advancements in technology, and the increasing need for efficiency but the workflow has not seen much in the way of fundamental innovation in the last 50 years.
This post will delve into the history of case picking, examine the industries that rely on this operation, and explore the technologies that have emerged to streamline the process. We’ll look at the aspects of case picking that still pose challenges today and the innovations that may shape the future of this critical warehouse activity.
The Origins of Warehouse Case Picking
Warehouse case picking refers to the process of selecting cartons or cases of product from a storage area to fulfill an order. While it may seem straightforward, case picking has undergone a transformation since the early days of industrial warehousing.
In the early 20th century, case picking was primarily a manual task, with workers (often referred to as “pickers”) walking long aisles in large warehouses to retrieve products. Warehouses were designed to store products in a way that maximized the use of space, but this often made retrieving individual items inefficient. Workers used paper-based systems to track orders and relied on basic tools like forklifts and hand trucks to move cases around. The manual nature of these operations was time-consuming and prone to human error.
As global trade expanded after World War II, the volume of goods moving through warehouses increased, necessitating better organization and more efficient retrieval processes. However, it wasn’t until the late 20th century that significant technological innovations began to emerge to optimize case picking operations.
But for large scale, expensive technologies that few can afford, case picking has remained largely the same since the 1980’s.
Industries That Rely on Case Picking
Case picking is a common operation in a wide range of industries, especially those that deal with large quantities of products and have frequent order fulfillment needs. Some of the most prominent industries that depend on case picking include:
Retail: Large retailers, both brick-and-mortar and e-commerce companies, heavily rely on case picking to move products from their warehouses to stores or directly to customers. Retailers handle a wide variety of products, and efficient case picking ensures that orders are fulfilled quickly and accurately.
Food and Beverage: The food and beverage industry often deals with perishable products that require fast and accurate handling. Case picking is used to select items like canned goods, beverages, and packaged foods, ensuring that products are delivered to supermarkets or restaurants on time.
Pharmaceuticals and Medical Supplies: In the pharmaceutical industry, precise case picking is crucial due to the sensitive nature of the products being handled. Medications must be picked and delivered with great accuracy, and compliance with safety regulations is essential.
Consumer Packaged Goods (CPG): CPG companies deal with high volumes of products like cleaning supplies, toiletries, and household goods. Case picking in this industry ensures that large orders are efficiently packed and shipped to retailers.
Third-Party Logistics (3PL): 3PL providers often manage warehouses for multiple clients across different industries, making case picking a central part of their operations. These providers must ensure that products are picked and packed according to the specific needs of their clients, making efficiency crucial.
How Case Picking Works
At its core, case picking involves retrieving specific quantities of product from storage locations within a warehouse to fulfill an order. The process typically consists of several key steps:
- Order Generation: Customer orders are generated, typically through an enterprise resource planning (ERP) or warehouse management system (WMS). These systems provide a list of items to be picked and the quantities required.
- Route Planning: In many warehouses, pickers are given a route or picking path to follow or are on their own to determine the best routes to hit their daily targets. Optimizing this path is critical to reducing travel time and increasing efficiency.
- Item Retrieval: Pickers move through the warehouse according to the selected route, retrieving cases of products from designated locations. In manual systems, workers may use paper lists or handheld devices to identify the products they need to pick.
- Order Consolidation: Once the items are picked, they are moved to a packing area where they are consolidated into an order for shipment.
- Shipping: The completed order is packed and prepared for shipping, ensuring it reaches the customer in good condition and within the promised delivery window.
Technologies That Have Enhanced Case Picking
The demand for faster and more accurate case picking has driven the development of numerous technologies aimed at optimizing this critical operation. Over the years, several key innovations have emerged, each improving upon the manual methods that dominated earlier warehouse operations.
Warehouse Management Systems (WMS)
One of the first significant technological advancements in case picking was the introduction of warehouse management systems (WMS). A WMS allows warehouses to track inventory in real time, manage orders, and optimize picking routes. By using a WMS, companies could reduce errors in the picking process, minimize inventory discrepancies, and improve order accuracy. These systems also enable better communication between different areas of the warehouse, improving overall efficiency.
Pick-to-Light and Put-to-Light Systems
Pick-to-light systems are designed to streamline the picking process by using visual indicators to guide pickers to the correct locations. In a pick-to-light system, lights are installed on racks or bins, and when a picker receives an order, the system illuminates the light corresponding to the correct product location. This reduces the need for paper lists or handheld devices and speeds up the picking process.
Put-to-light systems work similarly but are used during the packing process. When an order is being packed, the system lights up the correct bin or location where the item should be placed, ensuring that orders are packed accurately.
Voice-Picking Systems
Voice-picking technology, or voice-directed warehousing, was another major innovation in case picking. This technology allows pickers to receive picking instructions via a headset, freeing up their hands and eyes to focus on the task at hand. The voice system guides workers through their picking routes, reducing the time spent looking at screens or paper lists. Additionally, voice-picking systems often provide real-time feedback, improving accuracy and reducing errors.
Automated Storage and Retrieval Systems (AS/RS)
Automated storage and retrieval systems (AS/RS) represent a significant leap forward in case picking efficiency. These systems use automated robots to retrieve and store products in warehouses. AS/RS solutions are ideal for high-volume, high-density storage environments where maximizing space and reducing human labor is crucial. There are various types of AS/RS, including cranes, shuttles, and mini-load systems, each designed to handle different types of products and warehouse layouts. AS/RS systems can significantly reduce the time required to retrieve products and eliminate the need for pickers to travel long distances within the warehouse.
Robotics and Automation
Robotics and automation have become increasingly important in the world of case picking. Autonomous mobile robots (AMRs) and automated guided vehicles (AGVs) can transport products within a warehouse, reducing the need for human workers to push carts or drive forklifts. These robots can follow optimized routes and work alongside human pickers, significantly speeding up the picking process.
In addition to AMRs and AGVs, robotic arms have also been developed to handle the actual picking process. While robots have traditionally struggled with the dexterity required for picking individual items, advances in machine learning and artificial intelligence have enabled them to pick cases with increasing accuracy and speed.
Artificial Intelligence and Machine Learning
AI and machine learning are just starting to play a role in optimizing case picking. These technologies allow warehouses to predict demand, optimize inventory placement, and improve picking routes. Machine learning algorithms can analyze historical data to determine the most efficient ways to store products and route pickers, further reducing travel time and increasing overall efficiency.
Drones
Although still in the experimental phase, drones are being explored as a potential tool for inventory management and case picking. In large warehouses, drones could be used to quickly retrieve small items or to assist in locating products in high storage racks. While the technology is not yet widespread, it represents a possible future innovation in case picking.
Inefficiencies in Case Picking Today
Despite the technological advancements, case picking still faces several inefficiencies. These include:
Labor Dependency: While automation has reduced the need for manual labor, many warehouses still rely heavily on human workers. Labor shortages, high turnover rates, training costs, and safety incidents continue to be significant challenges.
Space Utilization: Even with advanced storage systems, maximizing the use of warehouse space while maintaining easy access to products remains difficult. Poorly designed storage layouts can result in inefficient picking paths and wasted time.
Order Variability: The increasing complexity of orders, particularly in e-commerce, makes it challenging to design systems that can handle a wide variety of products efficiently. High variability in order sizes and product types can slow down case picking operations.
Technology Integration: Many warehouses still struggle with integrating different technologies into a seamless system. A lack of communication between WMS, robotics, and other technologies can create bottlenecks and inefficiencies.
Current Technologies Are Insufficient
Current technologies that are in use today are insufficient to automate case picking operations for the market at large. Generally speaking, this tech falls into two categories.
Large-scale solutions like pick modules, case sorters, AS/RS and Goods-to-person solutions can produce massive productivity gains but they are expensive, enormously disruptive to deploy and can be inflexible to the changing needs of your case picking operations.
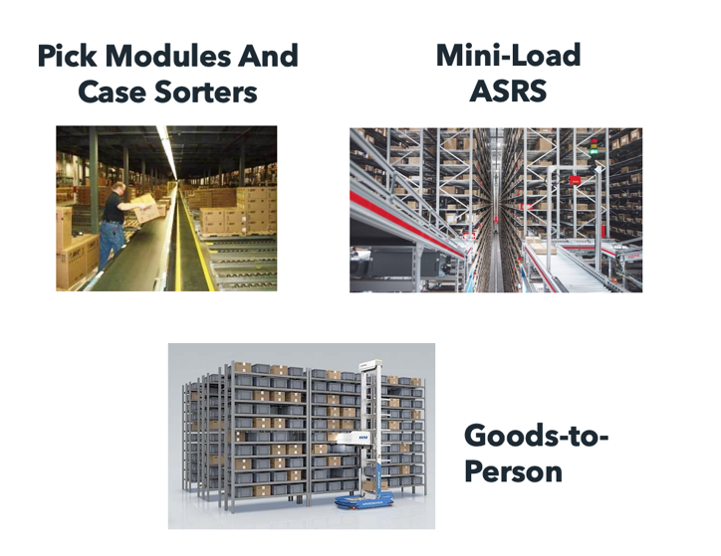
More flexible solutions like voice picking, semi-autonomous robots, and mixed-case robotic palletizers can be deployed rather rapidly at lower cost, but the productivity benefits of these technologies is marginal at best, and with high upfront costs, deliver weak ROI performance.
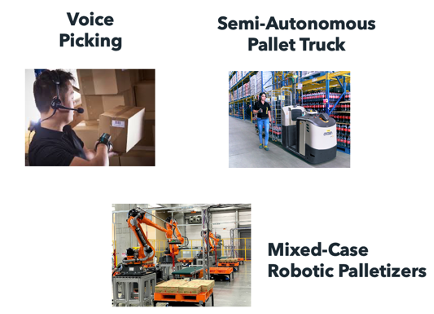
For more information on case picking inefficiencies
watch episode 7 of Robots vs. WildEnter CaseFlow™: A Revolution in Case Picking Automation
At Vecna Robotics, our approach to solving this problem was straightforward. Our team realized that the human work in case picking was vital to maintain flexible operations but that, somehow, the worker, the picklist, and the travel had to be decoupled to unlock massive productivity improvements. And that’s what we did.
Welcome to CaseFlowTM, case picking automation that orchestrates all aspects of your case picking operations to deliver greater than 2x performance gains and positive ROI in less than 12 months.
So, how does it work?
CaseFlowTM handles 90% of all workflow travel with robots (100% of pallet travel!) and focuses workers on picking more in dynamic zones throughout the day. Our powerful orchestration software manages it all: picklist prioritization from your WMS; robot path planning; and through a wearable, coordination with the picker about where to be and what to pick. It’s that easy.
Case Picking Before CaseFlow™
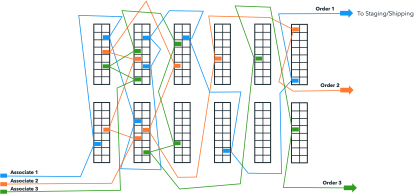
Case Picking After CaseFlow™
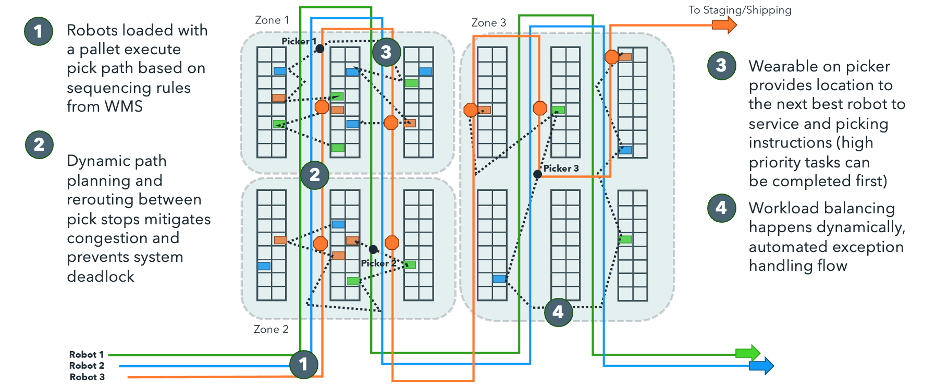
How is CaseFlow™ Different?
CaseFlowTM differentiates from other automation technologies across nearly every dimension.
The system uses your existing infrastructure, so you can get started right away. Through our Robots as a Service pricing, operations can get going with low up-front cost and the system can be deployed in as little as four weeks in parallel to existing case picking operations with minimal disruption.
Once the system is running, it can automate up to 90% of workflow travel with co-bot pallet jack robots, and our software then optimizes all case picking resources –– robots, people, and picklists –– to ensure maximum performance. With robots doing most of the travel and pickers focused exclusively on picking, your operation will need less pickers to deliver the same daily throughput.
With less than 2 weeks to get your pickers trained and the elimination of pallet travel from their workload, CaseFlowTM will reduce most travel-related safety incidents and will is technology that your pickers will love to use. And behind your team on the ground is Vecna’s 24/7 PivotalTM Command Center that ensures case picking operations are running at capacity all day. And the system was designed to be easily scaled up or down to handle the seasonal variability that most case picking operations experience.
CASE STUDY
GEODIS, has realized more than a 2x improvement in throughput since deploying CaseFlowTM at their pilot site in Indianapolis last year.
Is your operation right for CaseFlow™?
CaseFlowTM is ideal for case picking operations that:
- Have 10+ pickers today per shift
- Are running multiple shifts per day, 5+ days per week
- Move more than 2 million cases per year
- Have an average of units picked per hour per worker of ~150
- >80% of their picking is from ground
If you think CaseFlowTM is right for your operations and you would like to learn more go to our CaseFlowTM page here.
Want to run a quick ROI on your case picking operations? Check out our calculator here.
Ready to demo CaseFlowTM? Contact us today to arrange a preliminary call with a case picking automation expert today.