From No-Bot to Robot:
Installing Autonomous Material Handling Vehicles for Manufacturing or Warehousing in 5 Easy Steps
It is now well known that autonomous material handling vehicles (the next generation of automated guided vehicles or AGVs) are the best solution to supply chain disruptions, labor shortages and variable consumer demand. The problem for many of those yet to automate is not deciding whether to automate but knowing where to begin.
While this process may seem daunting, in fact, five simple steps will take you from no-bots to robots. You can get started on your automation journey today and have autonomous material handling vehicles operating in your facility in as few as three months. Read on to find out what a complete automation integration process looks like with Vecna Robotics.
Step 1: Assess
Every automation strategy is unique, just like every facility is unique. With an ever-evolving ecosystem of workflows and operations, your business will need a solution that is adaptable to realistic conditions. That’s why it is best to start with your most pressing pain points.
When it comes down to it, most autonomous material handling vehicles take on existing non-value-added travel. The recent boom in e-commerce has wreaked havoc on all kinds of material handling facilities, causing bottlenecks and lost efficiency in fulfillment, case-picking, milk runs and more. Repetitive, wasteful pallet movements become more costly each day. This is where automation, and our team’s expertise, really comes into play.
Once our team identifies pain points and automation opportunities in your facility, we get started on your assessment overview and ROI estimate. We’ll factor in conditions that affect your investment’s returns, which include the number of operating shifts, facility size, and layout (think ‘bigger is better’).
Following this initial assessment process, you’ll have the information you need to make a smart decision for your bottom line.
Step 2: Plan
After your facility has been scoped for automation, it’s time to dig a little deeper. We’ll look at key facility data that will show calculable, categorical improvement opportunities – specifically, factors like throughput, route convergence, and traffic density. When this information is applied to a CAD drawing of your facility, the solutions team can identify and plan the best routes for your autonomous material handling vehicles.
Now it’s time to test! Our experts use proprietary simulations to better visualize your outcomes. Here is what that process looks like:
- Select target workflow
- Perform simulation with realistic conditions
- Start with turnkey solutions and limited customization
- Initiate production use-cases
- Establish clear metrics and requirements
At the end of this analysis period, you’ll have a plan that determines the optimal size of your initial fleet, which workflows to automate first, the range of scalability available to you, and the system requirements you’ll need. Most importantly, you’ll have verified ROI and KPIs, and a set of benchmark goals that will measure your automation system’s success.
Step 3: Deployment

It is officially time to launch! In addition to providing major efficiency gains, AMRs require none of the disruptive or permanent infrastructural changes of legacy automation systems like Automated Guided Vehicles (AGVs). Instead, autonomous material handling vehicles integrate seamlessly into your operations and your existing WMS.
Our deployment team does the heavy lifting, taking care of the entire installation process from mapping and configuration to installation and optimization. Within days, your fleet is prepared to get to work.
However, while your facility is ready for robots –your employees might not be. At this stage, company attitudes can make or break your investment. A critical part of the deployment stage is employee onboarding. To facilitate integration, we familiarize employees with the technology through demonstrations and use-cases. Beyond official training and documentation, we also initiate proven methods to incentivize adoption.
KEY TIP: Test your integration early and often, and be sure to check in with employees frequently! You’ll want to monitor your staff’s patterns of usage and understanding of the navigation systems, as well as take suggestions for process improvements.
Step 4: Learn
Now that the fleet is up and running, the only thing left to do is let your robots learn! Our robots use the Pivotal Software Suite, a cutting-edge technology that enables self-learning capabilities. With Pivotal, the vehicles are able to share knowledge that fast tracks optimization.
The key to success at this stage is metrics – you can’t track what you don’t measure. Beyond our robots’ inherent data-gathering capabilities, we provide 24/7 support and monitoring with documentation of their progress and efficiency gains. Regular check-in meetings with our team will identify any changes that can boost performance, as well as opportunities for scaling. We encourage one maintenance check per year, as well as quarterly meetings to track ROI and business goal alignment.
Step 5: Scale
We know that scalability is the key to a successful automation investment, so we keep this in mind from the start. Every implementation starts with expansion in mind – meaning we keep track of network capabilities, workflow planning, shift scheduling, and opportunities for added robots. When you’re ready to expand your fleet, the learned knowledge of your operating robots will automatically be uploaded into your new robots. This means there are minimal disruptions for growth – it’s quick and easy. Even better, with our Robots-as-a-Service (RaaS) program, you’ll actually see more savings as your fleet grows.
KEY TIP: Share your ideas for expansion or improvement early so our team can get a head start on meeting your goals. Timing can be instrumental in maximizing ROI, and our team is happy to create preliminary estimates for additional automation projects.
Now, you’re in the big leagues. In five easy steps, you have installed autonomous material handling vehicles that operate with a 99% uptime. You’ll experience heightened levels of efficiency, reduced worker turnover, and market adaptability only made possible with automation.
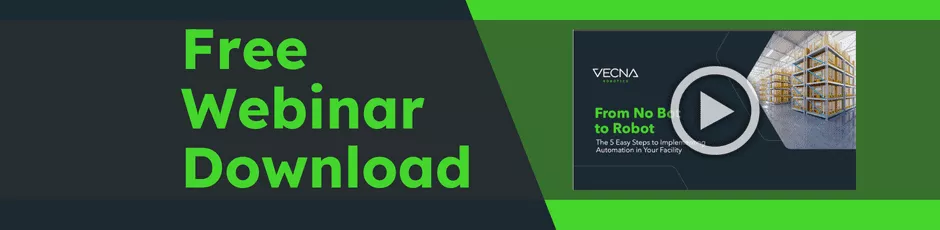
To learn more about getting from no-bots to robots, download this free webinar recording, or contact us and start your automation journey today.