Warehouse automation is no longer a luxury but a necessity for businesses aiming to stay competitive in today’s fast-paced world. The global rise in e-commerce, paired with heightened consumer expectations for quick and accurate deliveries, has placed immense pressure on the logistics industry. The race to streamline operations and optimize supply chains has propelled warehouse automation to the forefront of business strategies.
Additionally, as we’ve witnessed, unforeseen circumstances such as global pandemics, political upheavals, or economic downturns can severely disrupt supply chains. This has given rise to the trend of companies seeking resilience through automation. Automated warehouses are more adaptive, able to quickly recalibrate their operations in response to external shocks, ensuring minimal disruptions to the flow of goods.
Furthermore, the global labor market has been facing challenges, particularly in the warehousing sector. Finding skilled workers for manual tasks has become increasingly difficult, and retaining them even more so. Automation provides a solution by taking over repetitive and labor-intensive tasks, thus reducing dependency on human labor and, by extension, addressing issues related to labor shortages and rising wages.
Technological advancements, too, play a significant role. The decreasing cost of sensors, advancements in artificial intelligence, machine learning, and the rise of the Internet of Things (IoT) are making sophisticated automation solutions more accessible and affordable. This means that even small to medium-sized enterprises can now consider integrating advanced automation tools that were once the preserve of industry giants.
To analyze the current state of the material handling automation market, Vecna Robotics partnered with CITE Research to survey over 1000 supply chain professionals across industries including automotive, third-party logistics (3PL), consumer goods, manufacturing, e-commerce and retail to uncover the key trends, challenges, and opportunities in the market.
Before we dive into the details, here is a quick snapshot of the state of the market right now:
- Warehouses are facing a significant labor shortage – The majority of the market is 10-25% understaffed, with material handlers and forklift drivers to move pallets representing the largest labor gaps at 34% and 31% reporting difficulties in filling these positions, respectively.
- Automation is here to help – Most supply chain professionals view automation as a positive for workers, with 70% highlighting improved retention and over half recognizing it as a means to upskill employees and create new job opportunities.
- Autonomous pallet moving has just started to scale – Automation remains largely untapped, with 76% of companies having never deployed an Automated Guided Vehicle (AGV) and 70% never implementing an Autonomous Mobile Robot (AMR). Nevertheless, larger facilities are embracing automation, with 50% of those exceeding one million square feet having introduced AMRs. E-commerce leads the adoption rate at 39% with automotive closely behind at 38%.
- Case picking is everywhere – The majority of respondents (78%) are already using case picking in their operations, with a whopping 90% using it in the consumer goods industry, and yet this is still almost completely manually performed today.
By 2025, the global warehouse automation market is projected to expand to $69 billion. The following data will help us understand the drivers, barriers and financial considerations of adopting automation. In addition, the data informs how to achieve automation at scale to offset increasing product demand and global supply chain disruptions while keeping existing workers happy.
To deploy or not to deploy: That is the question
As a multitude of problems cripple the material handling industry, companies are turning to automation to help, with 85% of respondents planning to deploy some form of automation in the next 12 months.
Drivers for automation adoption
Unsurprisingly, the primary drivers for this adoption are the labor shortage (25%) and supply chain disruption (22%). Smaller facilities are particularly impacted by the labor shortage, while larger facilities are driven to automation due to supply chain disruption. Among industries, retail and e-commerce are most affected by the labor shortage and supply chain disruptions.
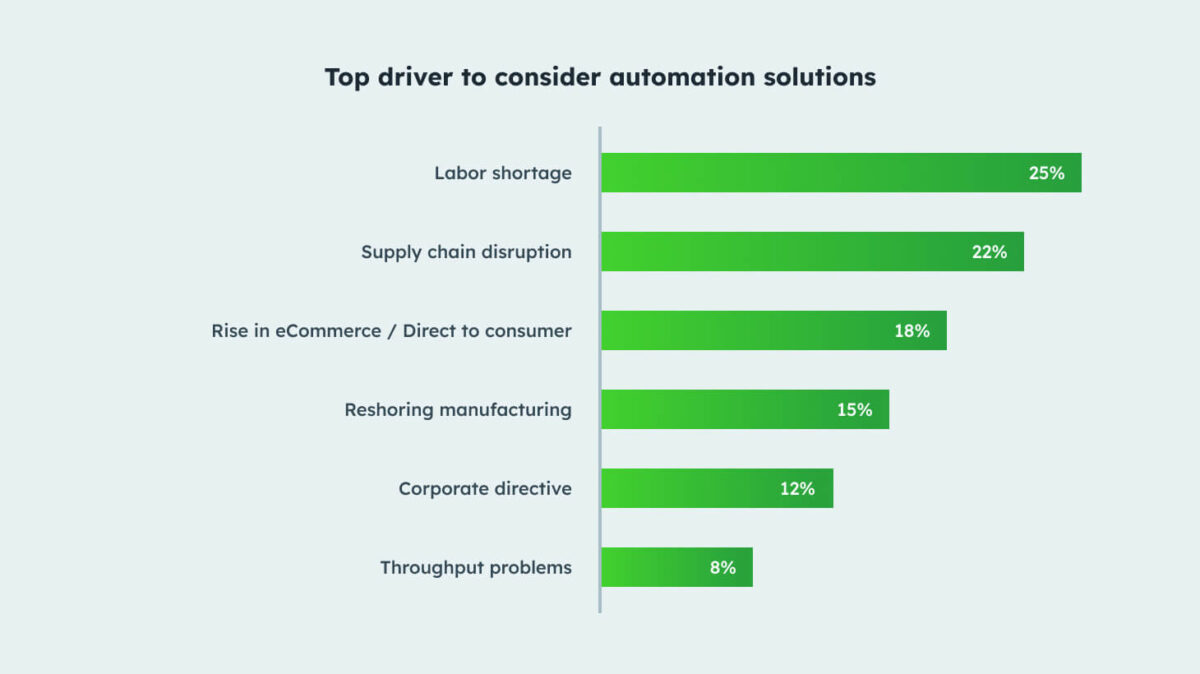
Barriers to automation
While it’s no secret that automation is gaining steam, with 4 in 10 reporting a strong return on investment (ROI) from previous deployments, there still remain a number of obstacles to adopting automation. Let’s dig into these.
In today’s volatile economy, cost concerns are at the top of the list of obstacles to implementing automation solutions, with budget (41%) and cost/ROI (40%) being the most significant. Cost/ROI was also the main obstacle to adopting automation efforts previously, with 54% of supply chain professionals stating that it has hampered their implementation plans.
Digging into the data, we discovered that all barriers to automation adoption show a negative correlation with facility size, except for cost/ROI. Surprisingly, the larger a company’s revenue, the more budget and cost/ROI become obstacles to adoption, which could reflect the following:
- Long term strategic vs. short term ROI: decision makers at larger firms may be under more pressure to show short-term returns to their business unit vs. smaller companies that have more runway to consider automation as a strategic long-term investment and competitive differentiator.
- Capex vs. Opex models: Dated capex cost models are delaying rapid adoption of automation at scale.
- Prove value: New technologies have to do a better job at proving value (no science projects please!) in environments with more financial discipline and in order to compete with other types of tech investments.
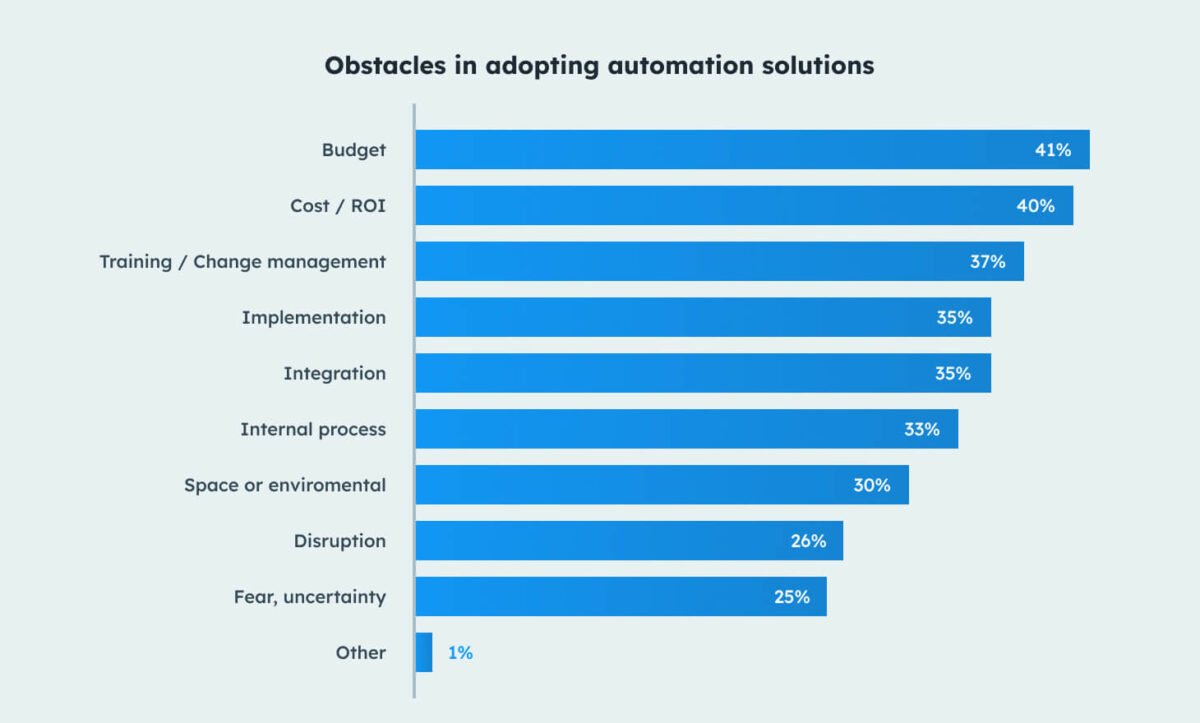
When it comes to adopting automation at scale, the barriers remain spread. Cost/ROI remained the top barrier (44%) but was followed closely by training/change management (43%).
Implementation complexity (39%), integration challenge (38%), and operational fit (38%) also represented significant barriers to adopting automation at scale.
Interestingly, facilities exceeding one million square feet behaved differently than the average-sized facility with their main barriers to adoption being performance, implementation complexity, integration challenges, and training/change management.
Our analysis also reveals that the 3PL industry is the least affected by these obstacles, while the consumer goods sector is the most impacted.
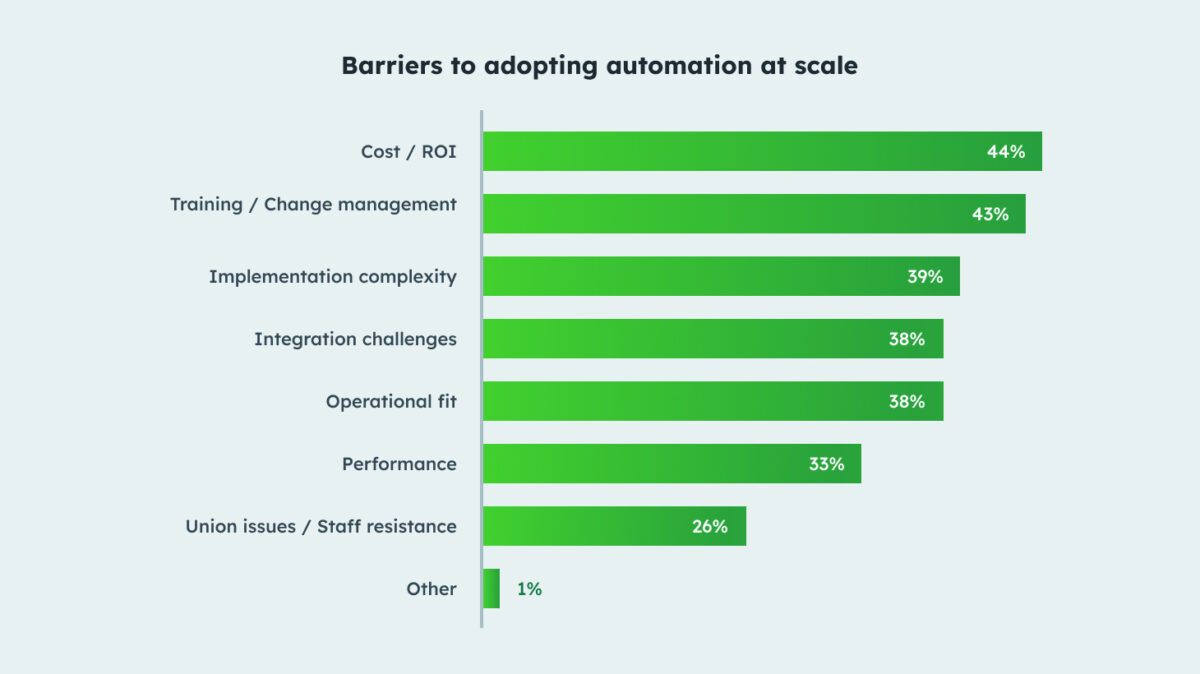
What technologies are facilities looking to adopt in 2023?
Automation isn’t the only technology top of mind for supply chain professionals. When asked to prioritize technologies for 2023, respondents shared the following feedback:
- 5G wireless is currently leading the way in deployment and is projected to have the most widespread adoption in the near term with 41% planning to deploy within the next 12 months. The manufacturing sector is poised to be a major adopter of this technology with close to 50% looking to deploy within the next 12 months.
- Technology information systems, such as Warehouse Management Systems (WMS) or Enterprise Resource Planning (ERP), were next on the list with 38% of warehouses planning to deploy in the next 12 months, with automotive (44%) and manufacturing (42%) set to be the biggest adopters.
- Battery and charging technologies followed closely with 37% of facilities planning to implement them in 2023, with consumer goods far outpacing the other industries in terms of adoption.
- Racking and storage equipment comes in fourth with 35% planning to deploy in the next 12 months, with consumer goods set to be the largest adopter (41%) and retail expected to be the lowest adopter (15%).
- Material Handling Equipment (MHE) robotics for pallet-sized loads is still in its early stages, with 31% of facilities surveyed planning to deploy in 2023. There is no real material difference across industries when it comes to pallet-sized robot adoption, with automotive set to be the largest adopter (36%) and retail expected to be the lowest adopter (22%).
Investing in automation
While MHE robotics is still in the early stages, it’s a promising prospect for the industry, so much so that almost 70% have budget earmarked for new material handling automation solutions within the next year. Let’s look at the financial considerations when adopting automation and who is making those decisions.
What are the financial considerations?
Understanding the financial dynamics surrounding warehouse automation is paramount. To truly comprehend the implications of the choice between CapEx and OpEx, one must first understand the fundamental differences. CapEx (capital expenditure) is an upfront cost, a significant investment that is expected to yield benefits over an extended period. It can be a harder pill to swallow for businesses with tighter cash flows or those wary of heavy initial investments without immediate returns.
On the other hand, OpEx (operational expenditure) allows businesses to spread the cost over time. This provides greater flexibility, and for many, is a more palatable approach when dealing with new and evolving technologies. With an OpEx model, businesses can quickly adapt to technological advancements without feeling tethered to an aging infrastructure.
Another noteworthy point is the involvement of upper management in CapEx decisions. Their involvement underscores the strategic significance of automation investments. But, securing their buy-in necessitates a well-crafted proposal, illuminating the long-term gains against the backdrop of the initial outlay.
Moreover, the leasing model, while traditionally effective for material handling equipment, doesn’t translate seamlessly to modern automation solutions. As technology evolves at a rapid pace, what’s cutting-edge today might become obsolete tomorrow. Thus, businesses must think beyond just the tangible equipment. They should account for intangible but essential elements like software integration, ongoing training, system upgrades, and potential scalability.
Ultimately, when considering the financial aspects of warehouse automation, supply chain professionals need a holistic view. By appreciating the hidden costs, understanding the broader financial landscape, and keeping an eye on the ever-evolving technological horizon, businesses can make informed decisions that align with their strategic goals and financial capacities.
Robotics as a Service (RaaS) models like those offered by Vecna, material handling robotics solutions are available as an annual operating expense enabling companies to update or increase their robot fleets as their needs evolve. RaaS models also tend to include all associated services and support, and are contractually bound to performance KPIs and uptime SLAs. We expect to see this flexible and scalable pricing plan become more common, with 84% of respondents saying that it would accelerate adoption. When looking at facility size, we found that the larger the facility or company, the more likely they are to adopt RaaS.
When building a cost model for automation solutions, companies most consider safety costs (48%), training costs (47%), turnover costs (42%), and/or labor availability costs (42%) in addition to just wages and benefits.
Breaking this down by facility size and industry, larger facilities are more sensitive to these cost factors. On an industry basis, the consumer goods industry is more sensitive to most cost factors.
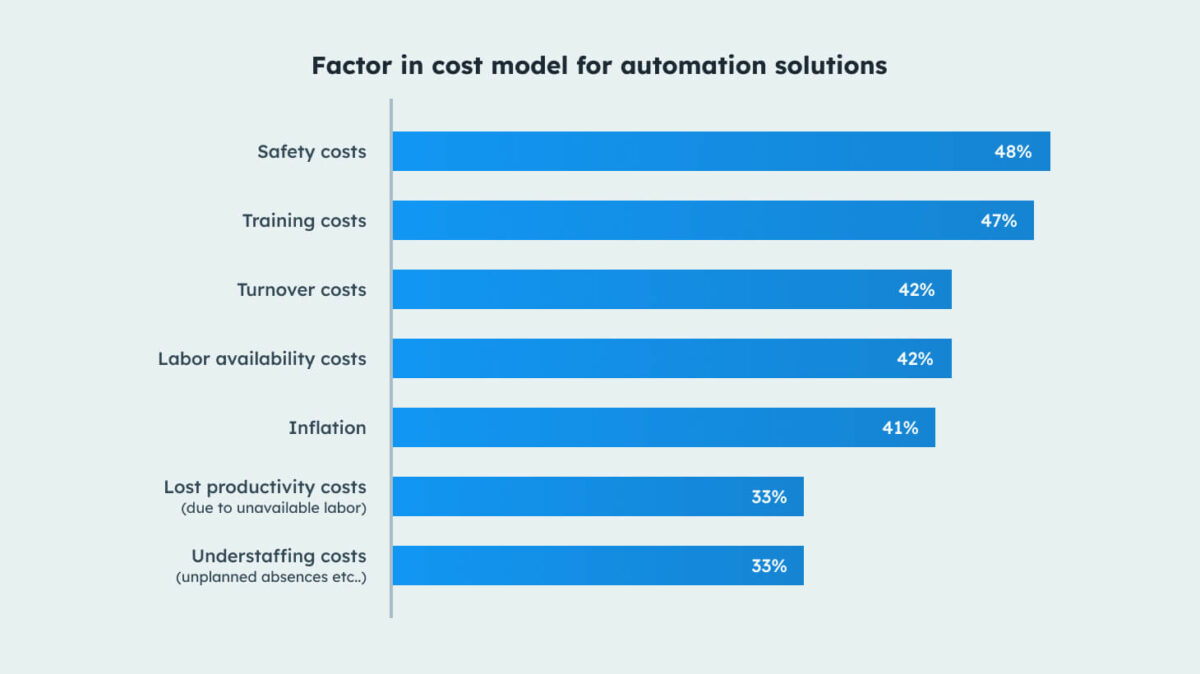
Who are the decision-makers?
Warehouse automation decisions, while rooted in technological implementation, carry implications that ripple across the breadth of an organization. Hence, the decision-making process encompasses a spectrum of roles that contribute unique perspectives to the table.
For instance, the Chief Operating Officer (COO) oversees overall operational processes, ensuring that any automation aligns with the company’s core operational goals. The Chief Supply Chain Officer (CSCO) focuses on optimizing end-to-end supply chain processes and ensuring that automation does not disrupt but rather enhances supply chain fluidity. Conversely, Chief Technology Officers (CTO) and IT departments are tasked with ensuring the technological feasibility of the automation projects and that they integrate seamlessly with existing systems.
Interestingly, for any material handling automation projects that are being considered, the majority of decisions (35%) are made by regional or line executives in charge of multiple facilities, while the next highest is a C-level decision at 25%.
When digging a little deeper, we see that:
- Finance, IT, and HR are more involved when facilities are larger
- IT is more involved in the decision-making within the consumer goods and manufacturing industries
- Corporate transformation/digital transformation was very influential when it comes to investing in automation in the consumer goods industry
- HR gets more involved in the decision-making process when the facility size or company’s revenue is larger
As we see above, the involvement of departments like Finance, HR, and IT becomes particularly salient in larger facilities. Finance evaluates the financial viability and potential ROI, ensuring that the investment aligns with fiscal goals. Meanwhile, the larger the organization, the greater the human capital considerations. Hence, HR’s involvement grows crucial to managing potential personnel implications, be it retraining, redeployment, or reskilling.
Specific industries also carry unique nuances. For instance, in the consumer goods sector, the ongoing wave of digital transformation significantly influences decisions. Such sectors see automation not merely as a means of efficiency but as pivotal in their transformative journey.
While the roles may vary in their degree of involvement, successful automation decisions are truly collaborative endeavors, weaving together a tapestry of insights from various organizational stakeholders.
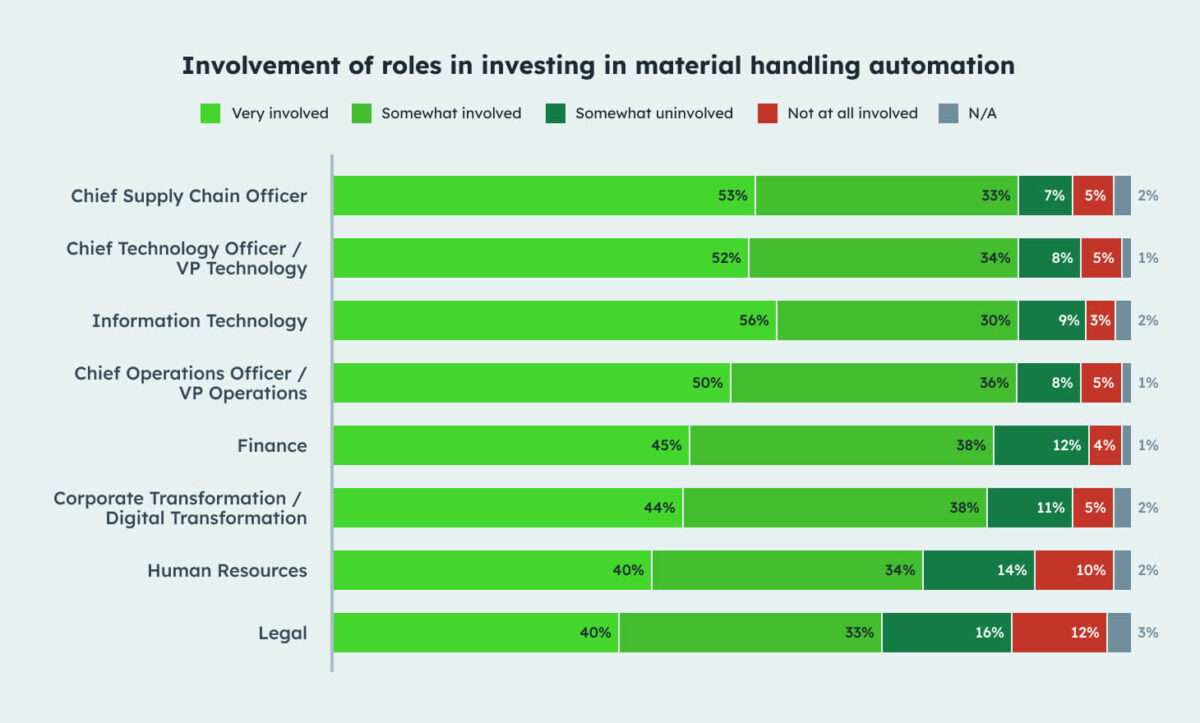
Getting to scale
So, how does automation become mainstream? Let’s look at what is affecting automation adoption at scale:
- The economic downturn is not significantly impacting adoption. 74% of automation projects are not impacted by fear of economic downtown. In fact, 15% are accelerating adoption. However, 26% of respondents reported that automation projects have been postponed or delayed indefinitely due to economic headwinds.
- Larger companies require a corporate strategic imperative to drive automation projects. Around 50% of companies with $1 billion or more in revenue rely on a corporate strategic imperative to adopt and scale automation.
- Increasing product demand and global supply chain disruptions are causing automation adoption at scale. Respondents cited increasing product demand (30%) and global supply chain disruptions (26%) as the largest factors in adopting automation at scale. Tightness in access to skilled labor (13%) and reshoring of production back to North America (11%) are less impactful.
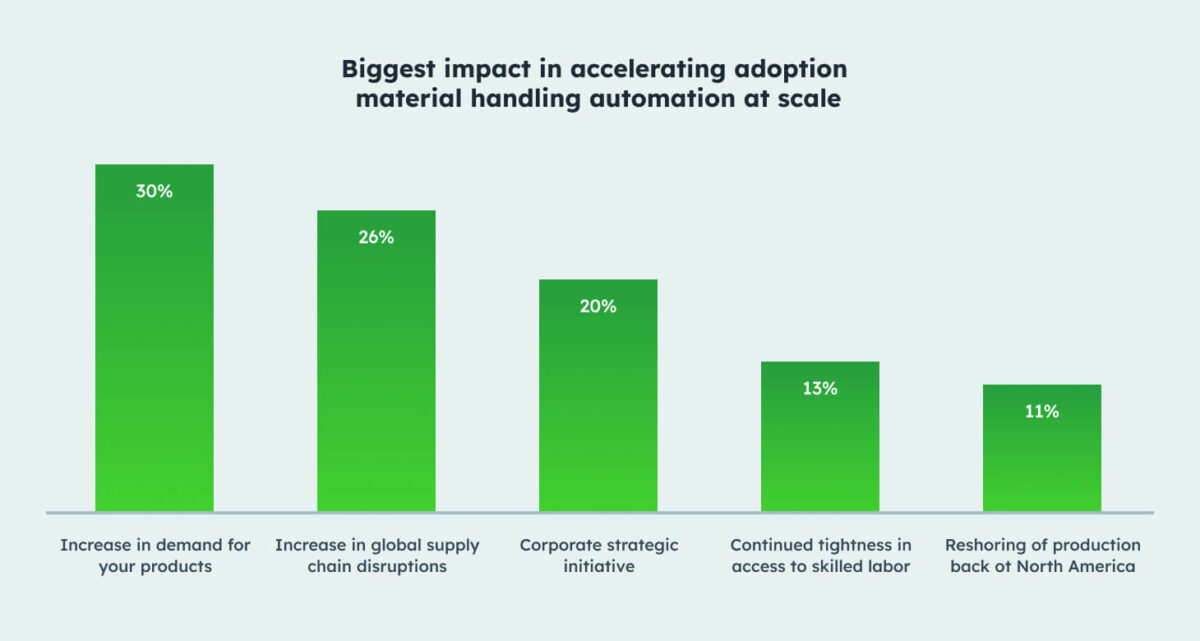
The robots are coming
The rapid ascent of automation in strategic discussions underscores a broader paradigm shift in the business landscape. Today’s competitive market pressures, coupled with the evolving consumer demand patterns, have necessitated a more agile, efficient, and adaptive operational approach. And automation sits at the nexus of this transformative wave.
Boardroom discussions, which once predominantly revolved around fiscal strategies and market expansions, are now echoing with debates on technological integration, especially in warehouse operations. Leaders recognize that the traditional methods of operation are becoming untenable in the face of growing complexities. Robots and advanced warehouse technologies are not just tools but catalysts for this change. They represent the convergence of efficiency, accuracy, and speed – elements vital for modern-day supply chain resilience.
Furthermore, this sense of urgency isn’t merely about staying ahead; it’s about survival. With each passing day, laggards in the automation journey risk being left behind, facing diminishing returns and operational bottlenecks. Conversely, early adopters stand to gain a competitive edge, fortified operations, and an enhanced ability to meet consumer demands promptly. Thus, the race to integrate robots and cutting-edge tech into warehouses is more than just a trend – it’s a defining movement shaping the future of commerce and supply chain operations.
Based on the data, following are the top automation deployment trends that we expect to see this year:
- High-speed, secure internet is the biggest technology obstacle for automation adoption so we will see the adoption of 5G Wireless technology as a main priority for companies. Updating and upgrading disparate WMS and ERP systems throughout supply chains and standardized across modern, cloud-based systems will also help alleviate some of the integration challenges currently faced by the industry.
- Consumer goods, automotive and 3PL will continue to lead the charge in automation adoption, with retail lagging behind.
- Due to the lack of labor in pallet-moving roles, automation will be increasingly sought after to augment the talent shortage, with case picking representing the largest automation potential.
- The largest facilities will deploy automation faster.
A broad look at the warehouse automation trends of 2023
From robotics and AI integration to innovative materials handling solutions, here we delve into the top warehouse automation trends that are revolutionizing operations and redefining efficiency.
- Robotics and Automation: The prevalence of robotics and automation within warehouse environments is ascending, offering a compelling avenue to elevate efficiency and productivity. The RIA’s data underscores this trajectory, revealing a significant surge in non-automotive robot orders in North America during the first quarter of 2021. A substantial 9,972 robots, valued at $485 million, were ordered—an impressive 19.6% uptick in units from the same period in 2020, and a 3.5% increase in value. These figures distinctly illustrate the growing imperative for robotics and automation to finely tune warehouse operations. From optimizing picking and packing to orchestrating control and monitoring across processes, these numbers emphasize the pivotal role of robotics in shaping the future of warehousing.
- Artificial Intelligence and Machine Learning: In 2023, the integration of AI (Artificial Intelligence) and ML (Machine Learning) into warehousing will emerge as a pivotal trend, significantly enhancing efficiency and accuracy. AI and ML algorithms, now applied to tasks like inventory management, order fulfillment, and predictive maintenance, redefine warehouse operations. AI-enabled robots with visual recognition and language processing skills adeptly locate and pick items, while ML-driven algorithms analyze sensor and IoT data, optimizing inventory and averting equipment downtime. This synergy ushers in a new era of agile warehouse management, characterized by faster, informed decision-making adaptable to real-time demands.
- Internet of Things (IoT): As warehouses strive for heightened efficiency and precision, IoT emerges as the linchpin by facilitating real-time monitoring and analysis, thanks to a network of sensors and interconnected devices. These IoT devices offer a plethora of functions, from meticulous inventory tracking to vigilant equipment performance oversight and even refining energy consumption.
- Automated Guided Vehicles (AGVs): The AGV market is expected to grow is growing at a rapid rate. With projections indicating its growth from a formidable USD 2.2 billion in 2021 to an impressive USD 3.2 billion in 2026, AGVs are fast becoming the backbone of contemporary warehousing. These vehicles, acting as the silent orchestrators, ensure seamless transportation of materials within the confines of warehouses and distribution centers, bridging the gap between various zones, facilitating pick-and-place operations, and even shouldering the responsibility of loading and unloading vehicles.
- Voice Picking: Transforming traditional picking methods, voice picking uses speech recognition for enhanced accuracy and productivity, emphasizing worker safety and improving order fulfillment. Powered by sophisticated speech recognition mechanisms, this technology meticulously deciphers voice instructions, offering instantaneous feedback and validation. Research and practical applications underline the efficacy of voice picking in augmenting picking precision, slashing errors, and turbocharging overall productivity.
- Autonomous Mobile Robots (AMRs): These robots excel not only in moving goods across expansive warehouse spaces but also in intricate pathfinding and obstacle avoidance through advanced navigation systems. Their integration with strict safety protocols ensures safe collaboration with human workers. AMRs’ impact transcends the physical domain; they’re also digitally empowered with cloud connectivity. This technological integration brings numerous benefits, including dynamic performance improvements, seamless software updates, and real-time analysis of performance metrics. Consequently, AMRs contribute not only operationally but also by providing valuable insights and adaptability in the evolving warehouse landscape.
- Blockchain: Essentially, blockchain offers a decentralized and transparent chronological database. This ensures all warehouse transactions are recorded and verifiable, preventing issues like double-spending or false reporting. From the entry of goods to their final shipment, every touchpoint is documented, reducing inefficiencies and disputes. Blockchain facilitates unprecedented collaboration among stakeholders. With shared ledgers, all supply chain participants, from material providers to end retailers, access real-time inventory data, fostering trust and enabling informed decisions.
- Augmented Reality (AR): The integration of Augmented Reality (AR) in warehousing marks a transformative leap in operational and training methodologies. AR glasses overlay digital data onto the physical environment, streamlining tasks and minimizing disruptions. For instance, during picking tasks, AR glasses provide unobtrusive guidance, enhancing efficiency and accuracy—crucial in peak periods and stocktaking. The shift toward a tech-savvy workforce is another incentive for AR adoption. Younger employees adapt swiftly to AR’s visual, interactive nature, expediting onboarding. Furthermore, AR aids in troubleshooting and maintenance, offering virtual guides to tackle machinery issues, reducing downtime and ensuring best practices.
- Cloud Computing: Cloud computing delivers unmatched agility, enabling warehouses to swiftly adapt to market shifts and customer demands. The capacity to dynamically scale resources, up or down, guarantees operational efficiency without substantial upfront investments. Beyond financial merits, cloud adoption spurs collaboration by centralizing data access. Teams across locations access up-to-date information, facilitating cohesive efforts. Cloud providers heavily invest in security, bolstering defenses against cyber threats. Additionally, seamless software updates ensure warehouses stay current with technology advancements.
- 3D Printing: 3D printing offers the ability to produce parts on-demand and minimizes reliance on external suppliers, averting disruptions. On-site production curbs the need for extensive spare parts storage, optimizing space management. And, as customization gains prominence, 3D printing meets personalized demands without mass production. This approach can reduce carbon footprints by minimizing part transportation.
For a more in-depth review and discussion about Vecna’s approach to deploying warehouse automation, watch our multi-part From No Not to Robot webinar series posted to our Resource page here: https://www.vecnarobotics.com/resource-filtering/?filter-resource-type=webinar
If you are ready to get started with an initial assessment, contact us today to set up an appointment with a Vecna Robotics automation expert.