AMR robots (Autonomous Mobile Robots) are revolutionizing the way warehouses and factories operate, providing operators with the advanced tools they need to meet rising customer expectations and increasingly intensified competition. In an era where speed, efficiency, and accuracy are paramount, an AMR robot is an indispensable asset. These vehicles support a wide range of applications in the modern warehouse and factory, including order picking, inventory management, and resupply requests, functioning as an integrated part of the supply chain process.
With an AMR fleet working alongside human operators on the floor, companies can create a synergistic environment where machines handle repetitive and precision-demanding tasks, and humans focus on more complex, cognitive functions. This collaboration can maximize productivity while reducing errors, allowing employees to concentrate on higher-value tasks that drive real business results. It’s not just about automation for efficiency’s sake; it’s about enhancing the human element of the workforce and creating opportunities for growth, learning, and innovation.
AMRs also represent a flexible and scalable solution, able to adapt to various operational needs and changes in demand. Their ability to integrate with existing systems, and the potential to reprogram them as needs evolve, makes them a future-proof investment. By leveraging this technology, businesses are positioning themselves to be more responsive to market fluctuations and more resilient in the face of unforeseen challenges.
In this article, we’ll look at some specific examples of how AMR robots work and their benefits.
First, what exactly are Autonomous Mobile Robots (AMRs)?
Autonomous Mobile Robots (AMRs) represent a pinnacle of robotic innovation tailored for complex and dynamic environments such as warehouses, factories, and even healthcare facilities. Unlike their predecessors, the Automated Guided Vehicles (AGVs), which follow fixed routes through magnetic tapes or wires, AMRs navigate using sophisticated sensors and artificial intelligence, allowing for flexible and intelligent movement throughout a facility.
AMRs are designed to understand and interpret their surroundings, making real-time decisions that allow them to reroute around obstacles or adjust to new layouts without requiring human intervention. This capability is grounded in technologies like LiDAR (Light Detection and Ranging), computer vision, and simultaneous localization and mapping (SLAM) algorithms. These technologies empower AMRs to create a digital map of their environment and navigate it autonomously, adapting as the environment changes or as their tasks shift.
The distinction between AMRs and AGVs lies in their level of intelligence and autonomy. AGVs typically require physical modifications to their operating environment to function correctly, such as the installation of tracks or markers. In contrast, AMRs can operate in unmodified environments, which significantly reduces setup costs and time. This flexibility makes AMRs particularly valuable in industries where layout changes are frequent or where the robot must be able to respond to dynamic operational conditions.
Types and Applications of Autonomous Mobile Robots
Autonomous Mobile Robots (AMRs) are not one-size-fits-all solutions; instead, they come in various types and models, each designed to address specific needs within diverse operational environments. The adaptability of AMRs to different tasks—from transporting materials across large warehouses to precise picking and sorting operations—highlights their versatility. Below, we explore some specific models of AMRs that exemplify this diversity and demonstrate the specialized capabilities that different types of AMRs can offer.
Stacker-Bot
Designed primarily for tasks involving stacking and storage, the Stacker-Bot is an AMR equipped to handle and organize inventory in warehouses. It operates by autonomously navigating to designated storage areas, and lifting and stacking goods to optimize space usage. The Stacker-Bot is particularly useful in high-volume distribution centers where efficient space utilization is critical. Its ability to stack items safely and precisely reduces the risk of inventory damage and enhances overall storage efficiency.
TiltSort-Bot
The TiltSort-Bot is specialized for sorting operations within distribution and fulfillment centers. This robot features a unique mechanism that allows it to tilt containers gently to sort items into appropriate bins or conveyor belts based on predefined criteria such as size, type, or destination. The TiltSort-Bot is instrumental in streamlining the sorting process, significantly speeding up operations and increasing throughput, especially during peak operational hours.
Hi-Tilt Bot
An advanced version of the TiltSort-Bot, the Hi-Tilt Bot offers enhanced capabilities for handling delicate items that require careful handling. Equipped with sophisticated sensors and precision control systems, the Hi-Tilt Bot can adjust the degree of tilt to minimize impact and ensure the safe handling of fragile goods. This robot is ideal for industries where handling breakable items is commonplace, such as in electronics or glassware distribution.
Go-Fer Bot
The Go-Fer Bot is designed to enhance fetching operations within various facilities. Whether it’s transporting parts across a manufacturing plant or delivering files within an office environment, the Go-Fer Bot helps reduce the time employees spend on menial transport tasks. With its high maneuverability and speed, the Go-Fer Bot efficiently navigates through crowded or complex environments, delivering items quickly and reliably.
The Technology Behind AMR Robots: Localization and Sensor Technology
Traditional “old-style” Automated Guided Vehicles (AGVs) represent an earlier phase in the evolution of warehouse and factory automation. These vehicles require some sort of physical infrastructure to navigate through their environment. The infrastructure could include wires, stickers, reflectors, tape, or magnets, or a combination of these elements. This necessity for physical cues means that any changes in layout or operations would require manual alterations to these guiding systems, creating significant downtime and labor costs.
In stark contrast, modern AMR robots signify a revolutionary step forward, needing no such infrastructure. Utilizing advanced technology like sensors, cameras, and sophisticated algorithms, they can recognize and navigate using natural landmarks like walls, pillars, or shelving to understand their location. This ability allows them to function more fluidly within existing environments and adapt more readily to changes.
AMR robots are designed to store a map of the facility in their digital memory, creating an internal blueprint of their surroundings. And when one AMR robot knows the map, it can share it with other AMRs, making the addition of more robots easy and quick. This interconnectedness among AMRs not only streamlines deployment but fosters collaboration among the robots themselves. If the facility changes, the map can simply be updated digitally, without the need for physical alterations.
This comparison between AGVs and AMRs illustrates a profound shift in the capabilities and flexibility of automation technology. While AGVs have their place, the rigidity of their design and reliance on physical infrastructure makes them less adaptable. Any desired change in an AGV’s path would require physical changes to the wires, tape, or other guiding systems, costing significant time and labor, not to mention the disruption of ongoing operations.
AMRs vs AGVs: Differences in Navigation and Control Systems
It can be broken down as simply as this: while AMR robots plan paths, AGVs follow them. Not only do traditional AGVs (Automated Guided Vehicles) need physical markers to tell them where they are, but those markers also rigidly define the pathway they are to travel. This inherent inflexibility manifests itself in the way they handle unexpected challenges in their environment.
What happens if an AGV encounters a lot of traffic, or an obstacle like a stray pallet, on that predetermined pathway? Traditional AGVs will simply stop and wait until the obstruction goes away. When faced with a stationary obstacle, it often means that human intervention is required. A worker must come to the rescue and remove the impediment, taking them away from their assigned duties and diminishing the usefulness of the automated vehicle. This rigid adherence to a set path without the capability to adapt to unforeseen circumstances can lead to inefficiencies and disrupt the flow of operations.
In contrast, AMR (Autonomous Mobile Robots) robots represent a more sophisticated and flexible approach to navigation. They plot out their paths using their internally stored map, typically choosing the shortest route. However, unlike AGVs, they possess the intelligence and adaptability to respond to changing conditions. If an obstacle blocks their pathway, AMR robots are smart enough to assess the situation and decide how to proceed.
They may determine that they can simply swerve around and circumvent the obstruction. If the AMR robot detects that a minor maneuver won’t work or isn’t safe, then it can plan an entirely different route to its appointed destination. This ability to dynamically re-route in response to obstacles not only avoids delays but can also optimize the path based on real-time conditions.
The impact on efficiency is clear. AMR robots require less human intervention to get their job done.
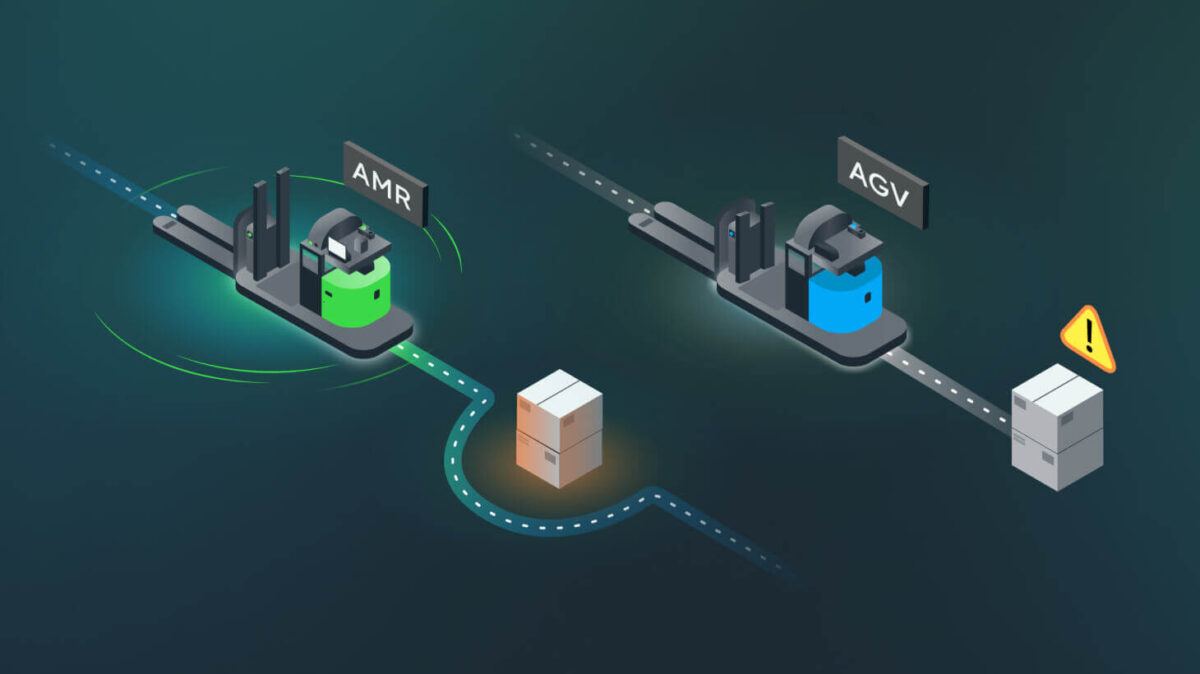
How an AMR robot can handle changing conditions
All mobile robots, whether traditional AGVs (Automated Guided Vehicles) or modern AMRs (Autonomous Mobile Robots), operate with safety zones. These zones ensure that robots maintain a minimum distance away from people or other vehicles before they operate at full speed. However, how these safety zones are managed and the flexibility in adapting to changes can vary greatly between AGVs and AMRs.
Traditional AGV vendors often attempt to define routes that allow for this safety buffer. However, this approach may become problematic when the environment changes or becomes more complex. Let’s say a loading dock was less well used when the AGV was installed, but as the facility starts operating at a higher capacity, some pallets start to be stored closer to the predefined AGV route. This proximity to the route can interfere with the AGV’s programmed safety zones.
To optimize safety, most AGVs will slow down to a crawl when they pass these pallets, as their pre-set safety protocols demand. Travel times lengthen as the AGV cautiously navigates the pathway, leading to reduced efficiency. If an operator decides to override the safety zone setting to maintain speed, it can become a significant safety risk, potentially compromising the well-being of workers and the integrity of goods.
AMR robots, on the other hand, are equipped with the intelligence and adaptability to respond to such situations with more nuanced strategies. They can simply give these protruding pallets a wider berth, recalculating their paths in real time. By doing so, efficiency and safety are both maintained without the need for human intervention or the risk of compromising either priority.
This ability to dynamically adjust to changes within the environment underscores the key difference between AGVs and AMRs. While AGVs rely on rigid predefined routes that may become suboptimal or even hazardous when conditions change, AMRs employ advanced sensors, algorithms, and artificial intelligence to continuously evaluate and respond to their surroundings.
AMR robots also have advanced pallet detection on their side
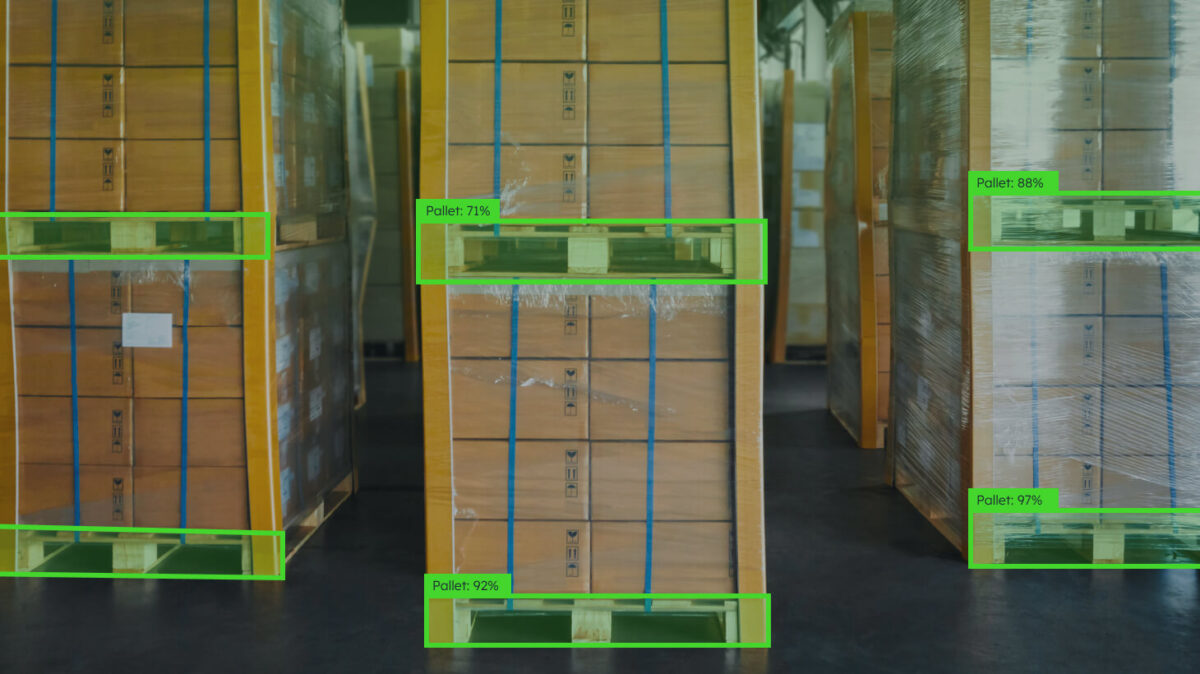
AMR Robots are far more adept than AGVs (Automated Guided Vehicles) in handling complex tasks like picking up pallets, especially in the domain of driverless forklifts where precision and adaptability are crucial. Having the AMR perform an independent pallet pick-up means that workers don’t have to interrupt their tasks to assist, creating a seamless flow in operations.
Even advanced AGVs have significant constraints on where pallets are located and positioned. Their rigid programming often requires exact placement. If the pallet is placed incorrectly, even slightly, it will frequently prevent the AGV from being able to engage the pallet. Then a human worker must intervene, leading to delays and inefficiency.
AMR robots, on the other hand, are equipped with computer vision, a technology that allows them to see and interpret the physical environment. They can recognize where the pallet is and adjust their approach accordingly, even if the pallet’s position isn’t exactly as prescribed. This ability yields massive efficiency improvements over AGVs.
Because the AMR robot can tolerate and compensate for slight inaccuracies in pallet placement, the collaboration between forklift drivers and the AMR robot is greatly enhanced. This not only accelerates the overall operation but also reduces the pressure on human workers to maintain absolute precision in their tasks.
Other Advantages of AMR Robots
As modern material handling increasingly adopts automation to enhance efficiency and reduce operational costs, Autonomous Mobile Robots (AMRs) are gaining prominence for their sophisticated capabilities. The advantages of AMRs make them particularly appealing in the diverse applications within the material handling sector.
Automation Flexibility
One of the standout advantages of AMRs is their remarkable flexibility in automation. Unlike traditional Automated Guided Vehicles (AGVs) that require physical modifications to the environment, such as tracks or magnetic tapes, AMRs are designed to navigate and operate independently using sophisticated sensors and mapping technologies. This autonomy allows them to understand and adapt to their surroundings dynamically, making them suitable for a wide range of environments without the need for extensive setup. This flexibility enables businesses to deploy AMRs in various sections of the supply chain, from warehouses to manufacturing floors, adapting to changes such as layout modifications or updated operational strategies with ease.
24/7 Operations
With the ability to operate round the clock, AMRs reduce downtime and significantly boost productivity. Their ability to work continuously without breaks or shift changeovers ensures that operations can keep pace with demand, especially during peak periods. AMRs are also capable of performing multiple tasks—from transporting goods to assisting in picking and packing processes—further streamlining operations and enhancing output. Their integration leads to a seamless flow of operations, allowing for quicker response times and less congestion within the operational areas.
Enhanced Safety
Safety is paramount in any operational setting, and AMRs contribute positively by reducing workplace accidents. Equipped with advanced sensors, AMRs can detect and avoid obstacles, ensuring safe interaction with human workers and other machinery. This proactive approach to safety reduces the risk of injuries and improves the overall safety of the work environment, fostering a more secure and efficient workspace.
Scalability
AMRs are highly scalable, providing businesses with the ability to adjust their automation level as their needs grow. The modular nature of many AMR systems allows for incremental investments, scaling up as the business expands or as operational demands increase. This scalability ensures that businesses can maintain efficiency and responsiveness without significant additional investment in new infrastructure.
Improved Accuracy
AMRs are equipped with advanced technologies that enable precise movement and operation, leading to improved accuracy in tasks such as inventory tracking, picking, and placement. This precision reduces errors, minimizes waste, and improves overall inventory management, which is crucial for maintaining the accuracy of stock levels and reducing discrepancies.
Environmental Adaptability
AMRs are adept at operating in a variety of environmental conditions, from cold storage to hot manufacturing environments. Their robust design allows them to function effectively across different climatic conditions, ensuring reliable performance regardless of the operational setting. This adaptability makes AMRs ideal for industries such as food and beverage, pharmaceuticals, and manufacturing, where environmental conditions can vary significantly.
Data Collection and Analysis
AMRs are not just operational tools but also data collection points that gather valuable information about operational processes. Equipped with various sensors, these robots collect data that can be analyzed to improve efficiency, predict maintenance needs, and optimize workflows. This capability transforms AMRs into integral components of an intelligent manufacturing or logistics system, where data-driven decisions lead to continuous improvement.
Economic Analysis: Expensive vs. Cost-effective
The financial implications of adopting Autonomous Mobile Robots (AMRs) in modern material handling operations are a pivotal consideration for businesses weighing the initial high costs against the long-term savings and efficiency gains. While the upfront investment in AMR technology can be substantial, the return on investment (ROI) often justifies the expenditure due to significant improvements in operational efficiencies and ongoing cost reductions.
- Initial Costs: the initial cost of deploying AMRs includes not only the purchase of the robots themselves but also the integration with existing systems and potential modifications to the warehouse or factory layout. These upfront expenses can be significant, making AMRs appear costly compared to traditional manual operations or even older automated solutions like AGVs. However, the scalability and flexibility of AMRs allow for incremental implementation, which can mitigate some of the financial burdens by spreading the investment over time.
- Operational Savings: Once in place, AMRs can dramatically reduce operational costs. Their ability to operate 24/7 without breaks or shifts means that they can achieve a higher throughput than human workers, reducing the time goods spend in the supply chain and increasing turnover rates. AMRs also minimize errors in tasks such as inventory management and order fulfillment, which further reduces waste and costs associated with returns or mis-shipments. The precision and efficiency of AMRs also mean fewer damages to goods and handling equipment, saving costs on repairs and replacements.
- Long-Term Cost-effectiveness: Beyond direct operational savings, AMRs contribute to long-term cost-effectiveness by enhancing workforce productivity. By automating routine and physically demanding tasks, AMRs free up human employees to focus on more complex and value-added activities, optimizing labor costs and increasing overall job satisfaction, which can reduce turnover and associated training expenses. Additionally, the data collected by AMRs can provide insights that lead to better decision-making, further optimizing operations and reducing wasteful practices.
AI also means continuous improvement over time
AMR robots boast greater onboard AI than traditional and even advanced AGVs, a technological advancement that significantly enhances their functionality and adaptability. Being cloud-enabled, they not only offer an immediate boost in efficiency but also open up an entire spectrum of continuous improvement and performance/safety optimization capabilities. These features were previously unpractical or entirely unavailable with more traditional AGV robots.
As the warehouse environment changes, AMR robots have the remarkable potential to learn, adapt, and improve over time. This continuous evolution allows them to optimize their performance, thereby increasing their throughput and useful life. It goes beyond mere task execution, enabling a proactive response to emerging challenges and opportunities within the warehouse landscape.
This ongoing adaptability also translates into significant ROI gains. The investment in AMRs becomes not just a fixed asset but a dynamic component of the operation that grows in value with time. By leveraging cloud connectivity and advanced AI algorithms, AMR robots align with modern Industry 4.0 principles, allowing companies to stay ahead in the competitive market. They embody a futuristic approach to warehousing where automation is not stagnant but continually evolves, ensuring that businesses can meet the ever-changing demands with agility, innovation, and sustained efficiency. The integration of AMRs signifies a profound shift in the warehouse automation paradigm, heralding a new era where machines are intelligent partners rather than mere tools, maximizing both operational efficiency and long-term value.
For more information on AMR robots and how they compare with traditional AGVs, consult our whitepaper titled “Everything You Need to Know About AMR Navigation”.
If you’re ready to get started with an initial assessment, contact us to set up an appointment with a Vecna Robotics automation expert.