The navigation of autonomous warehouse robots is the key performance indicator that will dictate the returns of investments in autonomy. Listen to Dr. Zachary Dydek, Chief Technology Officer at Vecna Robotics, speak about the intelligent technology that sets autonomous mobile robots (AMRs) apart from other automated solutions.
How Autonomous Warehouse Robots Navigate Industrial Facilities
While AMRs carry out the same functions as existing legacy automation systems like automated guided vehicles (AGVs), they do so using advanced navigation methods that allow them to vastly outperform other solutions. To first understand how they are able to do this, its important to understand how path-following AGVs traditionally operate. Like trains on a track, AGVs follow predetermined routes — typically using magnets installed in the floor or by tracking painted lines. Beyond the disruptive installation process that this entails, this means that the vehicles are limited and unable to adapt to anything that may interrupt their path. “With path-following, that’s all you can do,” says Dydek, “If something is in the way, it just stops and waits for someone to help.”
In comparison, AMRs are path-planners, meaning they use programmed intelligence to make decisions about where to go, and when. “They do more thinking, they understand how the world is connected,” says Dydek, “They reason about how to move in the facility like a person would.” With this technology, AMRs are able to negotiate space with better efficiency. Through the use of local sensors and onboard computing, they are able to navigate around other drivers and manual equipment, quickly figuring out the best possible response to their surroundings. “AMRs think like people and deal with challenges that invariably come up,” says Dydek, “Those challenges aren’t the exception to the rule – they are the rule.”
“It’s an important distinction. Path planning is a lot more flexible.” says Dydek on the benefits this navigation approach offers. He explains that AMRs have to look at the world and calculate how things move. When faced with other objects, an AMR will determine if it makes sense to leave its path and go around its obstacle by assessing how much time and space certain movements require. “It has to make some pretty complicated decisions to do that,” says Dydek, “It knows how to negotiate the space with other drivers or obstacles and still move quickly and efficiently.”
The Need for Intelligent Obstacle Avoidance
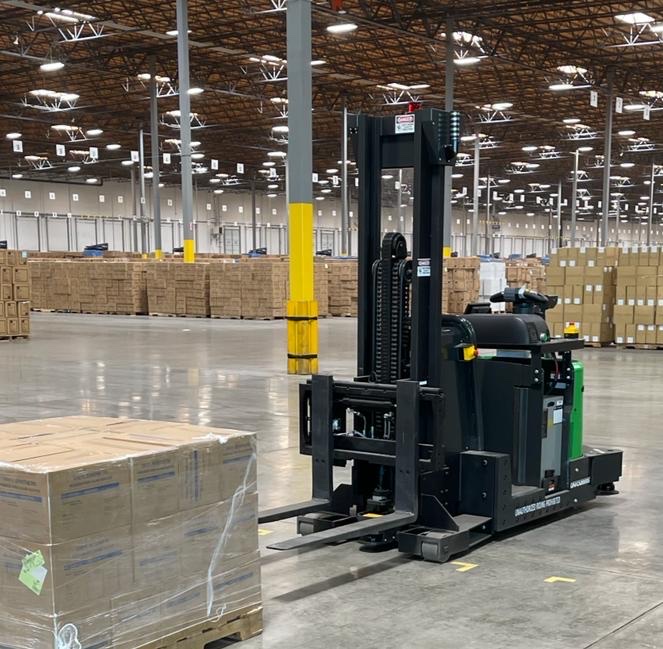
Dydek highlights the indisputable importance of obstacle avoidance and reasoning with data taken from operating facilities. He explains that 80% of the time, pallet movements carried out by Vecna Robotics’ pallet trucks require obstacle avoidance to make progress in their task. This means the robot can move more, save time and operate without human intervention. Without this technology, the robot would stop 80% of the time and wait for a worker to move the obstacle out of its way. “By having this feature, you’re really increasing the efficiency of the system,” Dydek explains, “You’re letting people do what people are good at, and allowing the robot to do its work.” In a dynamic environment like a warehouse, this heightened operational performance means an improved ROI on a shortened timeline.
Vecna Robotics is uniquely situated to exceed expectations with this technology. Being one of the more senior robotics companies in the industry provides an edge, but that’s not the only advantage the company holds. “We came at the problem from a different direction than AGV manufacturers,” says Dydek, “We started in an environment that is much more dynamic and much less structured than warehouses: hospitals.” He explained how Vecna’s original technology learned not only how to work with staff and navigate around hospital beds and equipment, but learned how to interact with individuals that had never seen a robot before. “When we came into the industrial space, we applied this technology. We have something a lot more flexible and better able to handle dynamic situations because of this.” Dydek explains.
Scalable Solutions with Easy Integration offer Adaptability
The aforementioned AGV installation process necessitates expensive and disruptive infrastructural updates. The opposite is true for AMRs. In fact, it’s so easy that the process can be conducted entirely remotely. Because they navigate using internal intelligent reasoning, the facility does not need to be altered in any way. Vecna Robotics’ AMRs share knowledge, so only one robot is used to map the facility to learn where pick-up and drop-off sites will be located. Dydek explains that this mapping method means an increased ability to scale the fleet with ease. “They download the knowledge and immediately start adding value.”
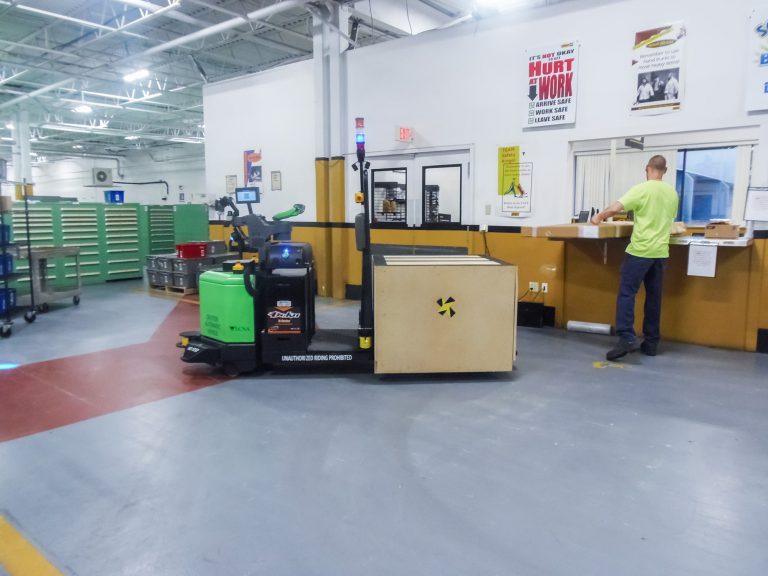
Vecna Robotics’ simple integration process was a key advantage to those automating throughout the last year, after supply chain disruptions and labor shortages left facilities struggling to meet surging consumer demands. “We are able to keep people focused on the tasks that are high value for people, tasks that require human creativity and ingenuity,” says Dydek on how this advantage extends to solving for the current labor shortage, “Let robots do the more mundane tasks like moving things around the warehouse, which takes a lot of time and staff.”
These economic pressures don’t seem to be going anywhere anytime soon. Many of the shopping patterns and expectations that end-customers adopted during the pandemic are here to stay. “There’s a lot of interesting changes happening, and a lot of them are going to stick around indefinitely.” says Dydek.
The key to overcoming the current challenges facing the material handling sector will be adaptability. In today’s turbulent times, Vecna Robotics autonomous warehouse robots provide technology that allows facilities to embrace the benefits of flexible automation.
Learn about how Vecna Robotics’ advanced technology offers a competitive advantage. Download The Complete Guide to AMR and AGV Navigation today.
See Vecna Robotics’ tuggers, fork trucks, and pallet trucks in action.