Automated Guided Vehicles, commonly known as AGVs, have evolved into a cornerstone technology for numerous industries, especially within warehousing, manufacturing, and logistics. The costs associated with acquiring AGVs can span a broad spectrum, influenced heavily by their intended use, the intricacy of the technology employed, and the material handling challenges they are designed to address.
At the entry level, AGVs can be procured for around $50,000. These are predominantly tailored for elementary tasks—think of transporting light items between distinct locations within a warehouse. Powered by batteries, their navigation primarily relies on rudimentary systems such as cameras or sensors, enabling them to traverse preordained routes.
However, as operations grow more complex, so does the need for advanced AGVs. More advanced AGVs, such as those designed for heavy payloads or specialized applications, can cost upwards of $300,000. These high-tier AGVs are often packed with superior technology, from sophisticated navigation systems that can self-correct and adapt in real-time, to robotic appendages that can handle intricate tasks. Some might even be customized for challenging operational environments, safeguarding them against excessive heat, moisture, or airborne particulates.
Beyond the vehicle’s initial outlay, prospective buyers must budget for supplementary costs.
- The installation process, for instance, varies in complexity and can see costs ranging from a few thousand dollars to an exorbitant sum for extensive systems.
- Maintenance, though inevitable, is another recurring expense. Components wear out, systems require updates, and occasional breakdowns need rectifying.
- There’s the often-overlooked expense of personnel training. Ensuring staff can proficiently operate and service these machines is paramount.
That said, it’s crucial to juxtapose these costs against the potential benefits. AGVs are celebrated for delivering remarkable ROI, largely by eliminating redundant manual tasks and optimizing processes. The ensuing uptick in productivity, coupled with potential savings in labor, often means that over time, the benefits derived from AGVs can far outweigh their initial costs.
The Evolution of AGVs
AGVs, or Automated Guided Vehicles, have experienced considerable technological growth, transforming their capabilities in warehousing, factories, and distribution hubs. Let’s delve into five pivotal advances shaping their evolution.
Navigational Upgrades – From Obstacle Interruption to Autonomous Rerouting: Historically, AGVs primarily followed fixed paths, often delineated using floor-based markings or specialized equipment. Encountering an obstruction would lead to delays, necessitating human intervention to resume operations. This system was cumbersome, especially in dynamic settings like factories where unpredictable obstructions are commonplace. However, the evolution of AGVs, particularly the emergence of Autonomous Mobile Robots (AMRs), has revolutionized this space. Modern AMRs possess internal maps, allowing them to circumvent obstacles and reroute autonomously. Vecna Robotics, a pioneer in this field, employs a cutting-edge navigation strategy that leverages superior localization and pathway design. This strategy not only ensures smoother operations but also significantly reduces manual interventions. Vecna’s research underscores this transformation, revealing that 80% of their AMR routes incorporated some form of obstacle avoidance, a significant step forward from traditional AGVs.
Enhanced Sensory Suite – Uplifting Safety and Navigational Precision: Earlier AGV models were restricted by basic proximity sensors. These sensors, though functional, provided limited insights into the surrounding environment. However, advancements in technology have brought forth AGVs equipped with an expansive array of sensors. These modern machines incorporate vision and LiDAR mechanisms, offering a comprehensive 3D perception of their surroundings. Such integrations, especially as exemplified by Vecna’s AGVs, enable these robots to navigate confidently even in bustling environments. To further refine its operations, Vecna has layered its machines with a multifaceted safety system. This system ensures that AGVs can adapt to varied operational needs while prioritizing safety, setting a benchmark in the industry.
AGV Interoperability – Seamless Robot Collaboration: The world of AGVs experienced a significant shift with the introduction of the MassRobotics Interoperability Standard by MassRobotics. This standard was envisioned to foster seamless interactions between robots, regardless of their manufacturer. Vecna Robotics, an early champion of this vision, has been actively collaborating with diverse robots, notably at a FedEx Ground facility. This synergy between robots of different makes and models introduces a plethora of operational advantages. For instance, it ensures that machines can efficiently exchange vital data, streamlining workflow. Furthermore, it offers organizations the flexibility to pick robots from different vendors while ensuring cohesive operations, marking a monumental leap in warehouse automation.
Human-Robot Symbiosis: There was a time when AGVs operated in isolation, with humans being advised to maintain a safe distance. This segregation was primarily due to the limited capabilities of earlier AGVs and the risk they posed. However, with technological advancements, the narrative has changed. Today’s AGVs are designed for collaboration. They are equipped with user-friendly interfaces, state-of-the-art safety mechanisms, and advanced obstacle-detection systems. Such features not only make AGVs more approachable but also create avenues for seamless human-machine interactions. The vision of workers collaborating effortlessly with machines, and utilizing advanced systems, is fast becoming a reality, reshaping the landscape of warehousing and manufacturing.
AI and Cloud Connectivity – Broadening Horizons: The integration of AI and cloud technology into AGVs has been transformative. Earlier AGV systems, though effective, were isolated in their operations. However, the contemporary landscape showcases AGVs that are constantly connected, tapping into the vast potential of the cloud. This connectivity ensures that AGVs receive real-time updates, enhancing their efficiency and minimizing disruptions. Furthermore, by connecting to the cloud, AGVs can harness the collective intelligence of an entire fleet. In the case of Vecna Robotics, this translates to each AGV leveraging the expertise of countless experienced operators. Such a collective approach accelerates learning, streamlines operations, and sets the stage for a future where machines are always evolving.
Types of Automated Guided Vehicles
AGV robots come in a plethora of shapes and sizes, each tailored for distinct operational needs. The right choice of AGV is determined by the specific requirements of the task at hand, the environment it will operate in, and the budget available. Here’s a list of the most common:
- Tow Vehicles (Tuggers): As the name suggests, these AGVs are designed to tow a variety of loads. Tuggers are used to pull carts that can be linked together in a train-like configuration, making them ideal for transporting materials around large facilities.
- Unit Load Carriers: These AGVs are built to carry assembled products, components, or larger items from one location to another within a facility. They come with flat decks or custom-fitted fixtures to hold the items securely during transportation.
- Forklift AGVs: These AGVs are designed to pick up and place heavy loads on shelves or racks. Their lifting mechanism allows them to transport, stack, and store pallets or containers, mimicking the function of a manual forklift but with automation.
- Pallet Trucks: Similar to forklift AGVs, pallet trucks are designed to transport pallets. However, they usually lift just enough to get the pallet off the ground and are commonly used for moving goods over short distances within a warehouse.
- Light Load AGVs: Built for speed and efficiency, these AGVs transport small loads quickly over long distances. They’re perfect for environments like hospitals or offices where they might transport mail, documents, or small parts.
- Assembly Line AGVs: These are specifically designed for assembly lines in manufacturing facilities. They are equipped with features that allow them to interact with machinery, aiding in the assembly of products.
- Compact AGVs: These AGVs are designed for tight spaces where navigation can be a challenge. Compact in design, they’re often used in crowded warehouses or facilities with narrow aisles.
- Autonomous Mobile Robots (AMRs): AMRs represent a leap forward in AGV technology. While traditional AGVs follow predefined paths, AMRs use sophisticated sensors, cameras, and algorithms to understand their environment, allowing them to autonomously navigate and avoid obstacles.
- Belt Load AGVs: These robots are equipped with a conveyor belt mechanism, making them perfect for continuous processes where items need to be moved from one conveyor to another, ensuring a seamless flow of products.
- Custom AGVs: For specific requirements not met by standard AGV types, companies can develop custom AGVs tailored to unique tasks, from specialized handling equipment to specific environmental resilience.
A new way to deploy automation: Robots as a Service (RaaS)
Robot as a Service (RaaS) is much like the familiar Software-as-a-Service (SaaS) pricing models in that it removes high upfront costs and rolls all fees into one, low regularly scheduled payment. This allows customers to realize ROI faster and does not tie up capital with a single lump sum payment.
While there are many benefits to RaaS pricing, the most important is shifting from Capital Expenditure to Operational Expenditure. Rather than having to gain executive-level approvals to purchase assets up-front, RaaS pricing requires a multi-term commitment (e.g., 3-year or 5-year) and a recurring annual payment model. This speeds up decision-making and allows for more efficient use of capital to deploy more robots faster, thereby realizing a measurable return on robotics within the first year. Another benefit of RaaS is that maintenance, support, and services costs are included which means that there are no downstream cost surprises and ensures mission alignment between the automation provider and the warehouse operator.
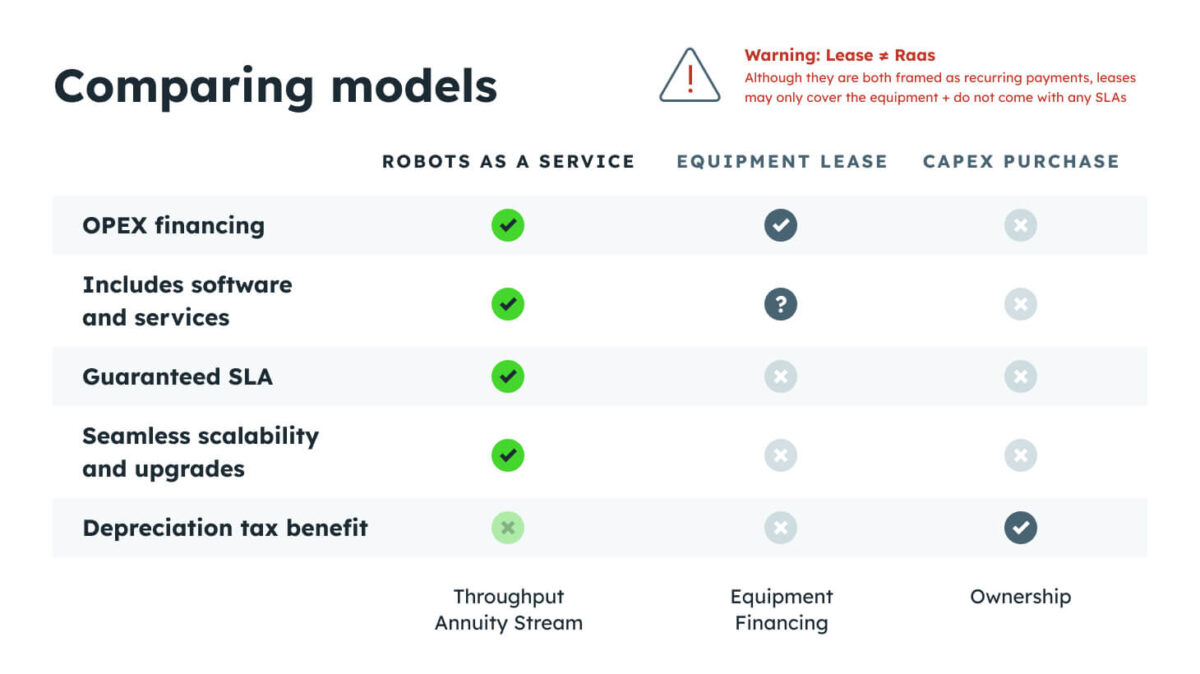
RaaS pricing has been around since the mid-2010s to reduce heavy, up-front investment for coworking robots, namely robotic arms in industrial and manufacturing environments. Small bots used for goods-to-person and person-to-goods conveyor applications more recently adopted the RaaS model as well. To date, no high-capacity autonomous mobile robot or AGV has offered Robot-as-a-Service pricing, instead preferring capital leases through 3rd parties.
However, with the growing demand for autonomous mobile robots (AMRs) and automated guided vehicles (AGVs), and concern about capital preservation, RaaS is beginning to show up in discussions around high-capacity self-driving materials handling equipment. Through an independent survey completed in October 2020, Modern Materials Handling found that 32% of warehouse and distribution center management say they are holding back on adopting AMRs due to a lack of capital. One month later, Tom Andersson of Style Intelligence market research published his findings, citing a major trend around rising interest in the robot as a service model for those in the market for autonomous pallet-moving vehicles in warehousing, manufacturing, and distribution centers.
Overall, the cost of AGVs (and AMRs!) varies widely depending on the specific application and the features and capabilities required. It’s important to consider all costs associated with implementing an AGV system, including installation, maintenance, support, and employee training. While the ROI of AGVs can be high due to the ability to automate repetitive tasks and increase productivity it’s important to pay attention to those downstream costs of keeping your system running properly in your total cost calculations. RaaS pricing models vastly simplify the automation buying experience and free up capital to deploy more automated throughput quickly and avoid any surprise cost as the system matures in years.
Vecna Robotics has a wide range of AMR pallet handling solutions designed to optimize warehouse operations with automation and improve overall throughput. Our solutions are available exclusively via Robots as a Service and allow you to deploy our AMRs for your most demanding warehouse workflows quickly. For more information about how to get your facility started with our automation solutions, go to our From No Bot to Robot page, or contact us today to schedule a consultation with a material handling automation expert.