Automation in manufacturing refers to the use of technology to automate tasks and processes, in order to increase efficiency, reduce costs, and improve product quality. Automation can be used in various stages of the manufacturing process, including material handling, assembly, testing, and packaging.
Benefits of automation in manufacturing
Since the world’s first industrial robot hit the production line in 1961, automation in manufacturing has grown from a novelty to an essential part of manufacturing efficiency. The benefits of automation in manufacturing increase year over year, as technology improves with more capabilities. These technological advancements enable new applications for robotics and improvements to how we already use robotics in manufacturing, helping facilities stay ahead of consumer demand. And between labor shortages, rising labor costs, and more cost-effective automation solutions, robotics in manufacturing are more viable than ever.
Types of manufacturing automation
Manufacturing comprises many complex processes, each requiring different automation capabilities. Here’s a look at the different types of manufacturing automation systems.
Fixed automation
Also known as hard automation, fixed automation refers to manufacturing systems that can be set to produce a single product in large quantities, with a high barrier of entry. The programming is typically contained within individual machines, bringing complex sequences and production operations together. Once set up, changing the process can be difficult and time consuming, often requiring the production line to be shut down. Examples of fixed automation in manufacturing include assembly lines, conveyor systems, and chemical manufacturing processes.
Programmable automation
Typically used for batch production, programmable automation refers to a system that runs on a set program, or a list of instructions that it uses to carry out specific operations. The benefit of programmable automation is that the program can easily be changed, but may require downtime to complete. Examples of programmable automation in manufacturing include industrial robots, numerically controlled (NC) machine tools, and programmable logic controllers.
Flexible automation
True to its name, flexible automation is characterized by its agility and flexibility. Like programmable automation, flexible automation systems rely on a program, but they have the capacity to perform changeovers automatically. Often, these programs are developed from a computer, allowing for remote monitoring and control. This means that flexible automation systems can be updated from anywhere at any time. Examples of flexible automation in manufacturing include material handling systems, robotics, and assembly lines.
Top 10 trends in manufacturing automation for 2023 and beyond
- Industry 4.0: The fourth industrial revolution, also known as Industry 4.0, is characterized by the integration of advanced technologies such as IoT, AI, and machine learning in manufacturing processes. This has led to increased automation and data exchange in manufacturing technology.
- Smart Factories: Smart factories, also known as Industry 4.0 factories, use advanced technologies such as IoT, AI, and machine learning to optimize production processes and increase efficiency.
- Robotics: Robotics is increasingly being used in manufacturing processes to automate tasks such as assembly, welding, and painting. Robotics, like Autonomous Mobile Robots, also allow for greater flexibility in manufacturing and can be easily integrated into smart factories.
- 3D Printing: 3D printing, also known as additive manufacturing, is a process in which a digital model is used to create a physical object by adding layers of material. This technology is being used in manufacturing to create complex and customized parts.
- Augmented Reality: Augmented reality (AR) is being used in manufacturing to provide real-time information and instructions to workers, making the manufacturing process more efficient and reducing the need for training.
- Internet of Things (IoT): IoT devices collect data on production processes, allowing for improved monitoring and control. IoT can also be used to predict maintenance needs and optimize production schedules.
- Artificial Intelligence (AI): The use of AI in manufacturing can optimize production processes, reduce waste, and improve efficiency. It can also be used to predict maintenance needs and optimize production schedules.
- Cybersecurity: As manufacturing processes become increasingly automated and connected, cybersecurity becomes a critical concern. Manufacturers are implementing measures such as network segmentation and monitoring to protect against cyber threats.
- Cloud Computing: Cloud computing can support manufacturing processes by storing, analyzing, and sharing data across multiple locations. This allows for improved collaboration and faster decision-making.
- Sustainability: Manufacturers are increasingly focused on sustainability, implementing measures such as recycling, reducing energy consumption, and using sustainable materials in the production process.
The role of autonomous mobile robots in manufacturing
AMRs (Autonomous Mobile Robots) are becoming increasingly popular in the manufacturing industry. These robots are designed to move around a facility and perform tasks such as transporting materials, assembling products, and performing inspections. AMRs have the ability to navigate around obstacles and work alongside humans, making them a versatile option for automating manufacturing processes.
One of the main benefits of using AMRs in manufacturing is their ability to increase efficiency. By automating the transportation of materials and products, AMRs can reduce the time and labor required for these tasks. This can also help to increase productivity and reduce costs. AMRs also have the ability to work around the clock, which can help to increase output and reduce downtime.
AMRs can also improve the accuracy and consistency of manufacturing processes. By using sensors and machine learning algorithms, AMRs can detect and identify products, components, and defects. This can help to reduce errors and improve the overall quality of the manufacturing process. AMRs can also be programmed to follow specific procedures, which can help to ensure that products are assembled or inspected according to industry standards.
Another benefit of AMRs is their ability to work alongside humans. AMRs are equipped with safety features such as sensors and cameras, which allow them to detect and avoid obstacles, including people. This makes it possible for AMRs to operate in environments where people are present, such as in warehouses, factories, and other manufacturing facilities. This can increase the flexibility of manufacturing processes, as AMRs can be used to perform tasks that may be too dangerous or difficult for humans.
AMRs can also be integrated into a facility’s existing systems, such as warehouse management software, to improve the overall efficiency of the manufacturing process. This allows for real-time monitoring and control of AMRs, as well as the ability to update tasks, routes, and schedules. This can help to optimize the use of AMRs and ensure that they are working to their fullest potential.
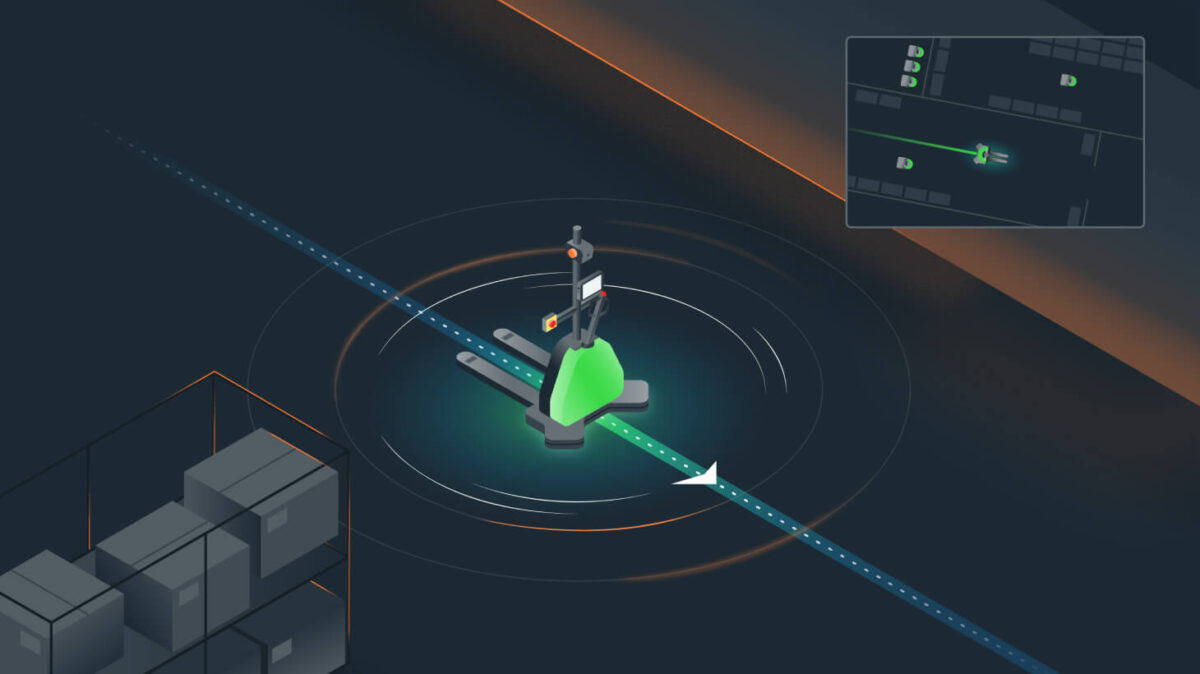
AMRs can also be used for a variety of manufacturing applications, including assembly, material handling, packaging, and inspection. In assembly applications, AMRs can transport and assemble components, which can help to reduce the time and labor required for these tasks. In material handling applications, AMRs can be used to transport materials, such as raw components, throughout a facility. In packaging applications, AMRs can be used to package and palletize products, which can help to reduce the labor required for these tasks. In inspection applications, AMRs can inspect products for defects, which can help to improve the overall quality of the manufacturing process.
Finally, AMRs can increase the flexibility of manufacturing processes. By using AMRs, manufacturers can quickly and easily adjust the production process to meet changing customer demands or market conditions. This can help to reduce costs, as well as increase the efficiency of the manufacturing process.
Automation in manufacturing is rapidly evolving, and the trend is to implement more advanced technologies such as IoT, AI, and robotics to optimize the production process, improve efficiency, and increase flexibility. Smart factories will become the norm, where IoT, AI, and machine learning are integrated to provide real-time data and intelligence for decision-making.
The focus on sustainability and cybersecurity will also be critical for manufacturers to meet the demands of the industry and consumers. Because of these trends, AMRs are becoming increasingly popular in manufacturing facilities. They’re versatile, nimble, efficient, and can work safely alongside humans, making them an ideal option for automating manufacturing processes.
Vecna Robotics has a wide range of AMR pallet handling solutions that can help you automate your manufacturing facility and warehouse. Our automation solutions are tailored for key manufacturing material handling workflows, helping improve your overall throughput. For more information about how to get started with our manufacturing automation solutions, go to our From No bot to Robot page, or contact us to schedule a consultation with a material handling automation expert.