Establishing how to run an efficient warehouse may seem straightforward at first, but the landscape of modern warehousing is far more complex than it appears. Warehouse managers currently face unprecedented post-pandemic challenges that make traditional operational strategies less effective. Among these hurdles are increasing workforce shortages and high consumer demand, both of which place immense pressure on an already strained system.
Warehouse automation represents a timely and innovative solution to these challenges. By employing cutting-edge technology, warehouses can achieve improved efficiency and a better pick rate. The use of automation not only streamlines daily tasks but also eliminates many of the human errors that can lead to inefficiencies. This means faster order processing, reduced labor costs, and the ability to meet consumer demands more effectively.
But the benefits of automation go beyond the immediate advantages. The potential for rapid scalability makes it a forward-looking solution that allows warehouse managers to adapt quickly to fluctuating market demands. Automation enables a more responsive and resilient warehousing system, positioning businesses to thrive in an ever-changing commercial environment. If you want to run an efficient warehouse, understanding and leveraging automation is no longer a futuristic concept; it’s an essential part of modern warehouse management.
1. Set up a warehouse management system
with a robust WMS module plays a pivotal role in modern warehousing, significantly increasing efficiency by indicating optimum pick-up and put-away methods. These intelligent systems not only streamline operations but also create automated pick lists for mobile devices, an enhancement that enables real-time updates and better communication within the warehouse.
With the appropriate WMS for your company, you will find that transaction accuracy improves, and picking errors decrease, leading to smoother workflow and satisfied customers. However, the selection of a WMS should be done with careful consideration of integration capabilities with other IT and automation systems. Cloud-based solutions can be a wise investment to avoid future upgrade and integration issues, offering greater flexibility and adaptability to evolving business needs.
Ensure that the WMS you choose aligns perfectly with your activity requirements, such as packing, stock control, put-away, and returns. Establish clear output requirements regarding dispatch documentation, management reports, labeling, and KPI monitoring; the chosen WMS should be tailor-made to fulfill these necessities.
Furthermore, support and training should be aspects to consider when selecting a WMS. Ensure that the vendor provides adequate assistance and training, as the success of the system depends on how well your team can utilize it. With the correct implementation and ongoing management, a WMS can become the backbone of your warehouse operations, leading to greater efficiency and profitability. Make sure the WMS is not only appropriate but also adaptable, scalable, and supportive of your long-term business goals.
2. Introduce barcode scanning
Labeling your products with barcodes is a pivotal step towards simplifying inventory identification and significantly reducing costly errors. By integrating stock-keeping units (SKUs) with barcodes, individual product identification becomes more straightforward, creating a smoother workflow within the warehouse.
To successfully implement this system, begin with an in-depth audit of your current products. Sorting them into specific categories and providing appropriate additional detail when necessary is essential. This categorization helps in managing the stock more efficiently and facilitates the barcode generation process.
Next, you will need to generate and print barcodes that correspond to each product’s unique details. Scanning and decoding each barcode’s information should be an integral part of the inventory management process. Modern barcode scanning technologies can be integrated with your existing warehouse management systems, creating a seamless information flow that provides real-time updates.
Once implemented, a barcode scanning system offers tremendous advantages. It saves time by automating the previously manual process of inventory tracking, reduces mistakes by minimizing human error, and improves traceability by creating an easily accessible digital record of each product’s journey through the warehouse.
But the benefits don’t stop there. In addition to efficiency gains, the implementation of a barcode system also enhances overall warehouse safety by enabling precise handling instructions and clear identification of materials. This leads to better compliance with regulatory requirements and fosters a culture of accountability within the team.
Investment in training and ensuring that all staff members are comfortable using the barcode system will further enhance its effectiveness. By turning a complicated process into a streamlined operation, a properly implemented barcode system becomes a foundational aspect of how to run an efficient warehouse, serving as a critical tool for improving accuracy and overall performance. It is more than just a method of labeling; it’s a comprehensive solution that supports and elevates your entire warehousing operation.
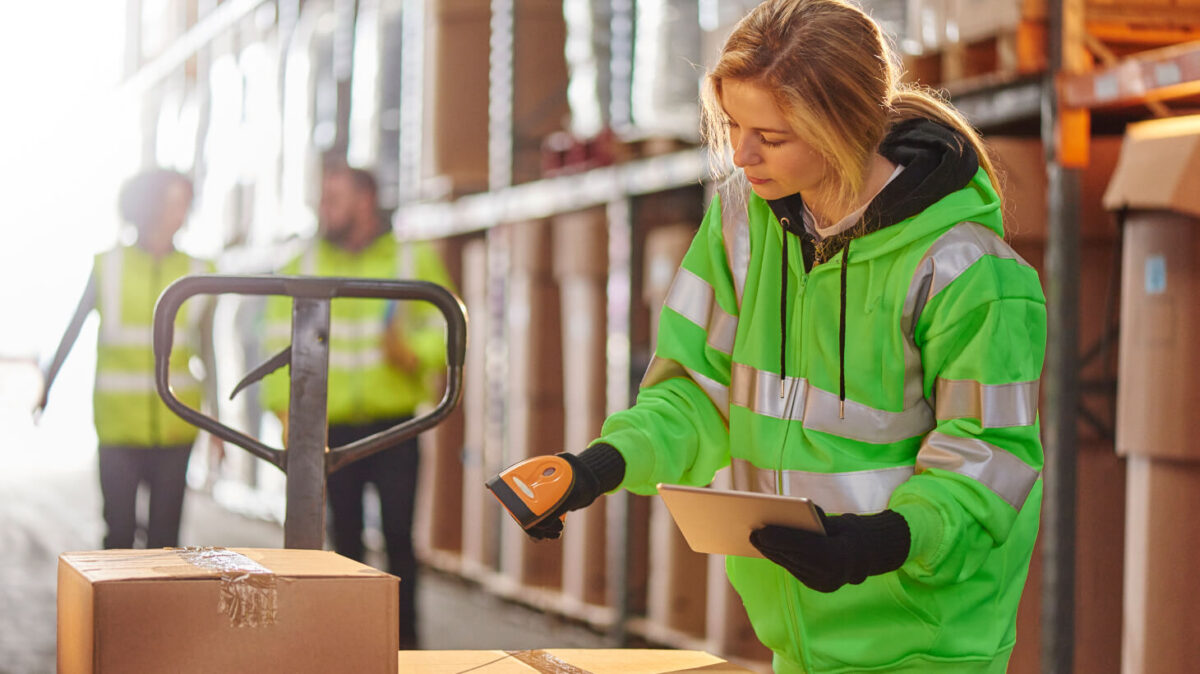
3. Optimize inventory management
Without an efficient inventory management system, costly errors inevitably increase as a business grows, leading to both financial losses and potential damage to customer relationships. In this technologically driven era, innovative solutions such as inventory drones and robots are transforming the way warehouses operate. Equipped with cutting-edge tools like radio-frequency identification (RFID) and barcode scanners, these automated systems can significantly reduce errors in inventory tracking.
When utilized in tandem with employee training, robotic solutions become part of a holistic approach to warehouse management. Proper integration ensures that robots and human staff work synergistically, each maximizing their unique strengths. Employees are freed from repetitive and time-consuming tasks, allowing them to focus on more complex and value-added activities, while robots handle the precision-driven tasks like scanning and sorting.
It’s essential to recognize that robotic solutions are not just about replacing human labor; they’re about enhancing it. With the correct labor and process systems in place, robots can increase accuracy, speed, and efficiency, thereby promoting a more effective warehouse management system.
Investing in a state-of-the-art inventory management system also creates an environment that’s more responsive to market changes. The agility provided by automated solutions ensures that warehouses can adapt quickly to fluctuations in demand or supply chain disruptions, maintaining a smooth flow of goods and minimizing delays.
The data collected through these automated tools can also provide valuable insights into inventory trends, patterns, and potential bottlenecks. This information can be leveraged for predictive analytics, allowing for more accurate forecasting and strategic planning. Managers can make more informed decisions and proactively address issues before they become significant problems.
The integration of technological solutions like drones and robots requires a careful balance and consideration of existing workflows, human resources, and overall business goals. Customizing these solutions to fit the unique needs of each warehouse will lead to the most effective implementation.
4. Increase warehouse visibility
Warehouse managers face the complex task of accurately forecasting supply, demand, and inventory. In today’s fast-paced business environment, traditional methods are often inadequate. As automated solutions are adopted, companies increase their warehouse activity awareness, enabling a more agile and precise approach to management.
Many automation solutions come equipped with advanced data analytics and order optimization software. Integrating these cutting-edge technologies into a Warehouse Management System (WMS) or Warehouse Execution System (WES) can provide a single source of record for all automated data streams. This integration doesn’t only enhance efficiency; it transforms how operations effectively monitor, manage, and measure each system. It allows for more insightful decision-making, tailored inventory control, and enhanced responsiveness to market changes.
Another innovative option to consider is a digital twin system. A digital twin provides a virtual sandbox, a digital replica of the physical warehouse, where new ideas are tested and improved before launch in the real world. This technology goes beyond simple simulations by leveraging real-time data to identify areas for streamlining within warehouse operations. It can analyze the potential impact of new strategies or changes in workflows, offering valuable insights without risking disruption in the actual operations.
The digital twin represents not just a step forward in technology but a leap into a new era of supply chain management. It’s set to be the next significant advancement, offering a proactive approach to optimization and forecasting. By creating an exact virtual representation of a warehouse, managers can explore different scenarios, predict potential outcomes, and make informed decisions with confidence.
In addition to these technological advancements, the human element should not be overlooked. Training staff to understand and utilize these advanced tools is crucial for maximizing their potential. Building a culture that embraces innovation and continuous improvement will ensure that the integration of automation and digital tools is not just about mechanizing processes but about elevating the entire operation to new levels of excellence.
5. Reduce safety risks
Standard warehouse operations traditionally involve high-risk activities, including heavy pallet handling and forklift truck operation. While workers can become quite skilled at these repetitive tasks, accidents are almost inevitable, and even minor incidents can be costly. The statistics paint a concerning picture; the average cost of each forklift accident is a staggering $188,000, not to mention the potential human toll.
With technological advancements, there are now viable alternatives to these high-risk activities. Automated guided vehicles (AGVs) and autonomous mobile robots (AMRs) can handle material handling tasks, effectively eliminating risks for warehouse employees. These machines are equipped with sensors, navigation systems, and intelligent software that allow them to perform complex tasks with precision and consistency.
The use of AGVs and AMRs also introduces a paradigm shift in warehouse workflows. Rather than employees moving to products, automation brings the products to the employee. This change in approach not only enhances efficiency but also reduces the likelihood of accidents by minimizing human traffic in busy areas.
The implementation of automated systems also often leads to a significant reduction in product damage. Machines are programmed to follow optimal paths and handle goods with uniform care, something that can be challenging to achieve with human operators. The resultant efficiency and accuracy contribute to both bottom-line savings and an overall more organized and controlled environment.
In addition to the immediate benefits in safety and efficiency, integrating AGVs and AMRs into warehouse operations has long-term implications for workforce development. By automating high-risk tasks, employees can be redeployed to more meaningful, complex roles that require human insight and judgment. This shift can lead to higher job satisfaction and the development of a more skilled and engaged workforce.
6. Improve product identification and sorting
Installing an automated sortation system in a warehouse setting is a transformative move that can yield substantial efficiency gains. This system, which automatically identifies and sorts products, is designed to streamline warehouse operations by utilizing sophisticated technology to handle a task that would otherwise require significant manual labor. The resultant decrease in order handling will not only improve workflow but also lessen growth constraints for your business, allowing for scalable operations.
An automated sortation system’s capabilities extend across various critical areas in a warehouse, including:
- Shipping Station: By automatically sorting products according to their shipping requirements, the system can ensure that the right products are sent to the correct destinations. This reduces shipping errors and expedites the entire shipping process.
- Packing Station: In the packing area, automation can intelligently direct products based on specific packaging needs, size, weight, or other criteria. This ensures that products are packaged appropriately and efficiently, minimizing waste and errors.
- Picking Zone: Automated sortation can significantly enhance the picking process by systematically directing products to the right zones. This can lead to reduced picking times and a more streamlined process, aiding in fulfilling orders more quickly.
- Returns and QA/QC Processing Zone: Automation in the returns and quality control areas can help in quickly identifying and sorting products that need inspection or reprocessing. This enhances the speed and accuracy of these critical processes, ultimately leading to higher customer satisfaction.
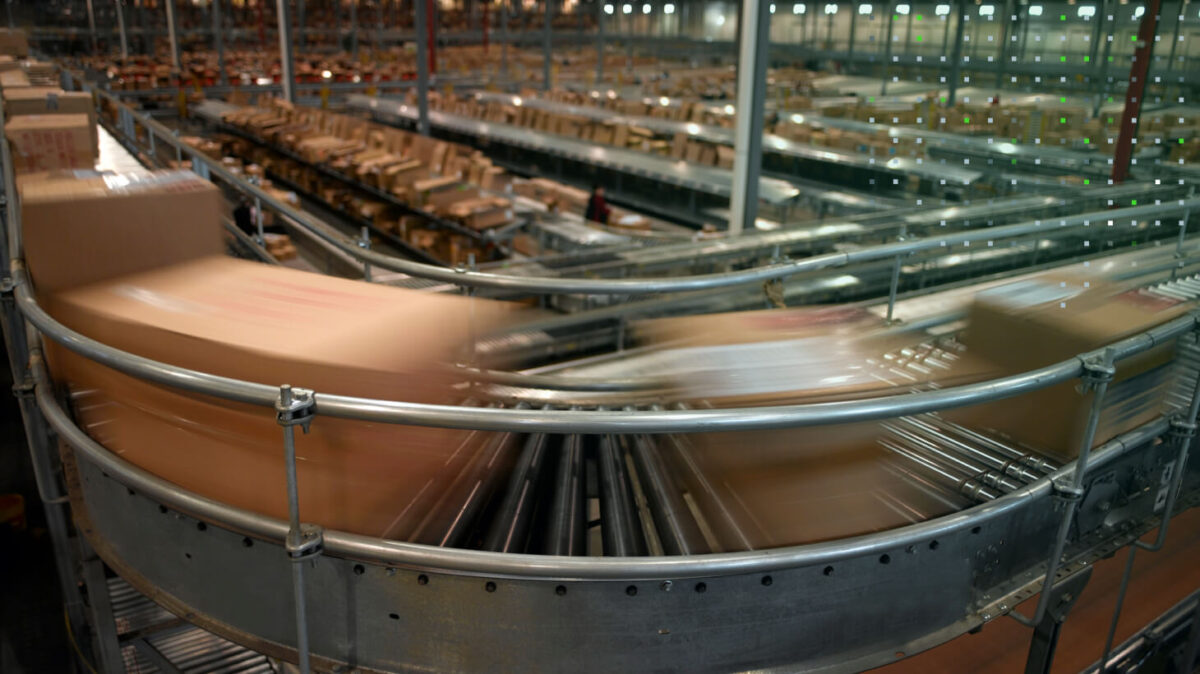
7. Invest in material handling automation solutions
You need not disrupt all your operations with costly Automated Storage and Retrieval Systems (ASRS) or other massive infrastructure investments. Instead, there’s a more accessible entry point to automation that can provide immediate benefits. Start automating the movement of goods in your facility to quickly find ways of making your existing labor more productive. This can be done without upending current processes or making large capital expenditures.
Autonomous mobile robots (AMRs), considered as the next generation or AGV 2.0, are incredibly flexible automation solutions that adapt quickly to any operation. Unlike traditional systems that may require extensive setup or permanent alterations to your facility, AMRs are designed to integrate seamlessly. Advanced AMR orchestration systems will navigate any facility without guidelines on the floor or human intervention. This adaptability means that they can be implemented with minimal disruption and customized to fit the unique needs of your operation.
Innovative Robots as a Service (RaaS) solutions are making the transition to automation even smoother. With RaaS, companies can access cutting-edge robotic technology without the significant upfront costs usually associated with such an investment. This service model ensures a super-fast transition from financing to deployment, with ongoing support and updates included. It’s a way to leverage the power of automation without being burdened by ownership, maintenance, or obsolescence risks.
Expect significantly increased accuracy and productivity once you adopt an AMR system. But beyond these immediate gains, consider the long-term strategic advantages. By automating routine tasks, your human workforce can be freed to focus on more complex and engaging activities, potentially leading to higher job satisfaction and retention. AMRs can also provide valuable data and insights into your operations, allowing for continuous improvement and more informed decision-making.
AMRs also offer scalability and flexibility that traditional systems might not. As your business grows or market demands shift, AMRs can be reprogrammed or redeployed to meet new challenges. This agility can be a critical factor in staying competitive in an ever-changing business landscape.
Conclusion
Implementing automation solutions within your business is a collaborative process that reduces human mistakes, operational time and costs, and safety risks. You’ll also see greater agility in order picking and storage. The ubiquity of the technologies has brought the time from adoption to cost down — now there is no excuse not to automate.
Let’s face it, labor markets have changed and the move to reshore/nearshore back to North America will only put more pressure on your ability to fill your productivity gaps. A healthy mix of automation investment today will make your current workers more productive by having them focus on value-added tasks that are better suited to humans. The longer a company’s transition time to autonomous operations, the harder it may be to catch up, especially as competitors begin their own automation journeys.
To learn more about how Vecna Robotics can help your distribution, warehousing, or manufacturing operations achieve its automation goals, click here.