The Era of Logistics Robots: Pioneers of the Next-Gen Warehousing and Distribution
In the whirlwind of technological advancements, logistics robots are stepping out of science fiction and into our warehouses and distribution centers, bringing with them a wave of transformation that’s hard to ignore. These robotic marvels aren’t just about heavy lifting; they’re redefining the very essence of supply chains and delivery systems around the globe. Whether it’s speeding up order fulfillment or navigating the vast aisles of inventory with uncanny accuracy, logistics robots are fast becoming the indispensable heroes of the warehouse floor.
In this guide to robotics in logistics we’ll dive into how these machines are solving industry challenges, revolutionizing safety standards, boosting efficiency, and shaping the future of logistics with every task they undertake. Join us as we explore the different types of logistics robots, the trailblazers leading the robotic charge, and how companies like Vecna Robotics are at the forefront of this exciting revolution.
What Are Logistics Robots? Understanding Definitions and Functions
Logistics robots are autonomous or semi-autonomous machines designed to perform tasks related to the movement, storage, and handling of goods within a warehouse, distribution center, or other logistics environments. These robots are equipped with advanced sensors, machine learning algorithms, and artificial intelligence (AI) that enable them to navigate complex environments, make real-time decisions, and interact with their surroundings. The primary goal of logistics robots is to improve efficiency, reduce operational costs, and enhance overall productivity in the logistics and supply chain industry.
Unlike traditional automated systems, which often require fixed infrastructure and predefined paths, logistics robots offer flexibility and adaptability. They can be easily integrated into existing operations without the need for significant modifications to the facility. This adaptability makes them an attractive option for businesses of all sizes, from small e-commerce companies to large multinational corporations.
Challenges Solved by Logistics Robots in Modern Industries
The logistics industry faces several challenges, ranging from labor shortages to increasing consumer expectations for faster deliveries. Logistics robots are designed to address these challenges and more.
- Labor Shortages: One of the most pressing issues in the logistics industry is the shortage of skilled labor. With the rise of e-commerce and the increasing demand for faster deliveries, warehouses and distribution centers are struggling to find enough workers to meet the demand. Logistics robots can help bridge this gap by automating repetitive and labor-intensive tasks, such as picking, packing, and sorting. For example, Amazon’s use of Kiva robots in their fulfillment centers has significantly reduced the need for manual labor while increasing efficiency and throughput.
- Operational Efficiency: Traditional logistics operations often involve manual processes that are time-consuming and prone to errors. Logistics robots can streamline these processes by automating tasks that were previously performed by humans. For instance, automated guided vehicles (AGVs) can transport goods within a warehouse, reducing the time it takes to move items from one location to another. This not only speeds up operations but also minimizes the risk of damage to goods.
- Error Reduction: Human error is a common issue in logistics, leading to misplaced items, incorrect orders, and delays. Logistics robots, equipped with precise sensors and AI, can significantly reduce these errors. For example, autonomous mobile robots (AMRs) used for order picking can accurately locate and retrieve items from shelves, ensuring that the correct products are picked every time.
- Cost Reduction: The high costs associated with manual labor, especially in regions with rising wages, can be a significant burden for logistics companies. By automating key tasks, logistics robots can reduce the reliance on human labor, leading to substantial cost savings. Moreover, robots can operate around the clock without the need for breaks, further enhancing cost efficiency.
- Space Optimization: Warehousing space is often limited and expensive. Logistics robots can optimize the use of available space by enabling high-density storage and efficient retrieval of goods. For example, robotic systems like shuttle systems and robotic storage and retrieval systems (RS/RS) can store items in compact spaces and retrieve them quickly when needed, maximizing the use of vertical space.
Are Logistics Robots Safe?
The safety of logistics robots is a critical consideration, especially as they operate in environments alongside human workers. Fortunately, logistics robots are designed with multiple safety features to ensure they can coexist safely with humans and other machines.
- Advanced Sensor Systems: Logistics robots are equipped with a variety of sensors, including lidar, cameras, and ultrasonic sensors, to detect obstacles and navigate their environment. These sensors allow robots to operate autonomously while avoiding collisions with objects, humans, or other robots.
- Real-time Decision Making: The AI and machine learning algorithms that power logistics robots enable them to make real-time decisions. If a robot detects an obstacle or a human in its path, it can quickly calculate an alternative route or stop to avoid a collision.
- Collaborative Robots (Cobots): In some cases, logistics robots are designed to work alongside human workers in a collaborative manner. These robots, known as cobots, are equipped with safety features such as force-limited joints that prevent them from exerting excessive force if they come into contact with a person. Cobots are designed to assist human workers rather than replace them, enhancing overall safety in the workplace.
- Regulatory Compliance: Logistics robots are often designed to meet stringent safety standards and regulations. For example, the International Organization for Standardization (ISO) has developed standards such as ISO 3691-4 for safety requirements of industrial trucks, including AGVs and AMRs. Compliance with these standards ensures that logistics robots operate safely and reliably.
- Training and Monitoring: To further enhance safety, many companies implementing logistics robots provide training for their employees on how to interact with these machines. Additionally, robots can be monitored remotely to ensure they are operating correctly and safely.
What Are the Benefits of Logistics Robots?
The adoption of logistics robots offers a wide range of benefits that extend beyond simple automation. These benefits have the potential to transform the logistics industry by improving efficiency, accuracy, and overall operational performance.
- Increased Productivity: Logistics robots can perform tasks at a much faster rate than humans, leading to increased productivity. For example, robots can work 24/7 without the need for breaks, ensuring continuous operation and maximizing throughput.
- Enhanced Accuracy: The precision of logistics robots in tasks such as picking, sorting, and packing reduces the likelihood of errors. This leads to improved order accuracy, fewer returns, and higher customer satisfaction.
- Scalability: Logistics robots offer scalability, allowing companies to easily adjust their operations to meet changing demands. During peak seasons, additional robots can be deployed to handle the increased workload, and they can be scaled back during slower periods.
- Cost Efficiency: While the initial investment in logistics robots can be substantial, the long-term cost savings are significant. Reduced labor costs, lower error rates, and increased productivity all contribute to a more cost-efficient operation.
- Flexibility: Logistics robots are highly adaptable and can be programmed to perform a variety of tasks. This flexibility allows companies to reconfigure their operations quickly in response to changing business needs.
- Improved Workplace Safety: By automating hazardous tasks, such as handling heavy loads or working in extreme conditions, logistics robots help improve workplace safety. This reduces the risk of workplace injuries and associated costs.
Types of Logistics Robots and Industry Leaders
The logistics industry has seen the development of various types of robots, each designed to perform specific tasks. Below are some of the most common types of logistics robots and the companies leading the way in their development.
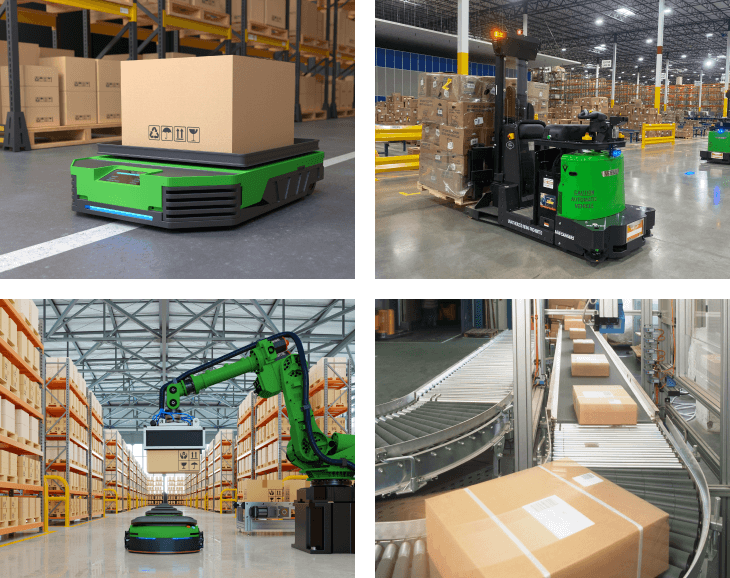
- Automated Guided Vehicles (AGVs): AGVs are used to transport goods within a warehouse or distribution center. They follow predefined paths and are often used for tasks such as pallet transportation and conveyor integration. Industry leaders in AGVs include Dematic, JBT, and Daifuku.
- Autonomous Mobile Robots (AMRs): Unlike AGVs, AMRs do not rely on fixed paths and can navigate dynamically within a facility. They are used for tasks such as order picking, goods transportation, and inventory management. Companies like Locus Robotics, Fetch Robotics (acquired by Zebra Technologies), and Vecna Robotics are prominent in the AMR space.
- Robotic Arms: Robotic arms are used for tasks that require precision, such as picking, packing, and assembly. These robots are often used in conjunction with vision systems to identify and manipulate objects. Industry leaders in robotic arms include ABB, KUKA, and FANUC.
- Shuttle Systems: Shuttle systems are used for high-density storage and retrieval of goods. They operate on rails within a racking system, quickly retrieving items for order fulfillment. Leaders in this space include SSI SCHAEFER, Mecalux, and Kardex Remstar.
- Drones: Drones are increasingly being used in logistics for tasks such as inventory management, surveillance, and last-mile delivery. Companies like DJI, Matternet, and Wing (a subsidiary of Alphabet) are pioneering the use of drones in logistics.
- Collaborative Robots (Cobots): Cobots are designed to work alongside human workers, assisting with tasks that require dexterity or collaboration. Companies like Universal Robots, Rethink Robotics (now part of HAHN Group), and FANUC are leaders in the cobot market.
6 Industries Capitalizing on Logistics Robotics
Logistics robots have become an integral part of various industries, each benefiting from the efficiency, accuracy, and cost savings these robots bring. The application of logistics robots extends far beyond traditional warehousing and distribution, impacting sectors such as e-commerce, manufacturing, retail, healthcare, and even agriculture. Here’s a closer look at how different industries are utilizing logistics robots and the specific tasks they perform:
- E-commerce: The e-commerce industry is perhaps the most visible user of logistics robots. With the massive increase in online shopping, companies like Amazon, Alibaba, and JD.com rely heavily on logistics robots to manage their fulfillment centers. Robots in e-commerce are used for tasks such as order picking, packing, sorting, and even last-mile delivery. The speed and accuracy provided by these robots help e-commerce companies meet tight delivery windows and handle high volumes of orders, particularly during peak seasons like Black Friday and Cyber Monday.
- Manufacturing: In the manufacturing sector, logistics robots play a critical role in material handling, assembly line operations, and inventory management. Automotive manufacturers, for instance, use automated guided vehicles (AGVs) to transport heavy parts across the production floor, reducing the time and labor required for these tasks. Robotic arms are used for precision tasks such as welding, painting, and assembling components, improving product consistency and reducing errors.
- Retail: Retailers are increasingly adopting logistics robots to optimize their supply chains and distribution networks. In distribution centers, robots are used to pick and pack products, manage inventory, and ensure that goods are delivered to stores or customers in a timely manner. Walmart, for example, uses robotics in its distribution centers to handle repetitive tasks, allowing human workers to focus on more complex activities.
- Healthcare: The healthcare industry is another area where logistics robots are making an impact. Hospitals and medical facilities use robots to transport medications, medical supplies, and even patient meals. These robots help reduce the burden on healthcare staff, allowing them to focus more on patient care. Additionally, logistics robots are used in pharmaceutical manufacturing and distribution, ensuring that drugs are handled and delivered safely and efficiently.
- Agriculture: In agriculture, logistics robots are being used to automate tasks such as planting, harvesting, and transporting crops. These robots help farmers increase productivity and manage their fields more effectively. For example, drones are used to monitor crop health, while autonomous tractors and harvesters perform labor-intensive tasks with greater precision and efficiency.
- Food and Beverage: The food and beverage industry utilizes logistics robots for tasks such as packaging, palletizing, and transporting goods within factories and warehouses. These robots help ensure that products are handled hygienically and efficiently, meeting the stringent standards of the industry. Companies like Coca-Cola and Nestlé use robotics to streamline their production lines and improve overall operational efficiency.
Whose Got the Top Bots? How Vecna’s Logistics Robots Drive Warehousing and Distribution Efficiency
Vecna Robotics is a leading player in the logistics robotics industry, known for its innovative solutions that enhance efficiency, flexibility, and safety in warehousing and distribution environments.. Vecna’s robots are equipped with advanced AI and machine learning algorithms that enable them to navigate complex environments, make real-time decisions, and adapt to changing conditions. This high level of autonomy allows Vecna’s robots to operate seamlessly alongside human workers, enhancing overall productivity and reducing the need for manual intervention.
Here are some of the unique benefits that Vecna Robotics’ logistics robots bring to warehousing and distribution:
- Flexibility and Scalability: Vecna’s robots are designed to be highly flexible and scalable, making them suitable for a wide range of applications and environments. Whether a company needs to move pallets, transport goods between different areas of a warehouse, or handle order picking, Vecna’s robots can be easily adapted to meet specific needs. This flexibility also allows businesses to scale their robotic fleet up based on demand and growth needs.
- Seamless Integration: Vecna Robotics emphasizes the importance of integrating its robots into existing operations without disrupting workflows. Their robots are designed to work with existing warehouse management systems (WMS) and enterprise resource planning (ERP) systems, allowing for smooth coordination between robotic and human workers. This integration capability reduces the time and cost associated with implementing robotics in a warehouse or distribution center.
- Collaborative Robotics (Cobots): Vecna’s robots are designed to operate safely alongside human workers. These collaborative robots, or cobots, are equipped with sensors and safety features that allow them to work in close proximity to people without posing a risk. This collaboration enhances productivity by allowing robots to handle repetitive or physically demanding tasks while human workers focus on more complex and value-added activities.
- Real-time Optimization: Vecna’s robots are not just autonomous; they are intelligent. The company’s AI-driven platform enables real-time optimization of robotic operations, ensuring that tasks are completed in the most efficient and effective manner possible. This real-time decision-making capability allows Vecna’s robots to respond dynamically to changes in the environment, such as sudden increases in order volume or unexpected obstacles, ensuring continuous and smooth operations.
- Data-driven Insights: One of the standout features of Vecna Robotics is its emphasis on data and analytics. The robots collect vast amounts of data during their operations, which can be analyzed to gain insights into warehouse performance, identify bottlenecks, and optimize processes. This data-driven approach allows businesses to make informed decisions that can lead to significant improvements in efficiency and cost savings.
Vecna Robotics has established itself as a leader in the logistics robotics industry by delivering solutions that are not only technologically advanced but also practical and impactful. Their focus on autonomy, flexibility, and data-driven decision-making sets them apart from other players in the market. As more companies look to automate their warehousing and distribution operations, Vecna Robotics’ innovative solutions will continue to play a crucial role in shaping the future of logistics.
Logistics robots are revolutionizing the way industries operate, offering solutions to some of the most pressing challenges in warehousing, distribution, and beyond. With industry leaders like Vecna Robotics driving innovation, the future of logistics looks set to be more efficient, flexible, and sustainable than ever before. As these robots continue to evolve, their impact on the global supply chain will only grow, making them an essential component of modern business operations.