Flexible Automation Alleviates Logistics Pressures Caused by Non-Conveyables
Over the course of the last few years, many in the industry have come to view material handling automation as revolutionary and necessary technology. This is in part due to an extreme, sustained, and unpredictable jump in e-commerce and non-conveyable shipments. Non-conveyables (bulky goods such as appliances or furniture that are too big to fit on traditional conveyors) once accounted for a fraction of total shipments, but now make up almost 15% of direct-to-consumer supply chain goods. This demand-shift has had a notable and disruptive impact on many logistics organizations’ traditional workflows.
Before this shift, companies could temporarily solve problems caused by non-conveyables by throwing more people into the mix. As non-conveyables increase in number, this solution becomes less and less practical. The true solution? Flexible automation.
Flexible automation – made possible by self-driving, autonomous mobile robots (AMRs) – turns troublesome non-conveyable loads into efficient transports. AMRs eliminate repetitive, manual operations while offering flexibility in what’s moved and when. Robotic solutions are highly scalable and do not require infrastructure changes, making for an easy installation process and the ability to increase or decrease use as needed. With programs such as Vecna Robots-as-a-Service program, organizations can lease robots and adjust their fleet size without hassle.
Using Material Handling Automation to Improve Efficiency
Matt Cherewka, director of business development and strategy at Vecna Robotics, spoke with Inbound Logistics, explaining how Vecna Robotics’ AMRs are able to adapt to their environment and streamline operations.
“They plot multiple potential routes and choose the most efficient option based on factors like distance, traffic, and location of the stops along the route,” Cherewka says. “When necessary, they can reroute on the fly.” He also discusses Pivotal, Vecna Robotics’ groundbreaking, multi-agent orchestration engine. Pivotal works similarly to a warehouse management system, but uses advanced algorithms to balance demand and dynamically assign tasks to both humans and robots, improving throughput and raising the robotic fleet’s ROI significantly.
Trending Growth of Automated Equipment Adoption
Warehouse automation has been growing in popularity. Integrating robots into warehouse workflows increases productivity and maximizes throughput. Forbes reports that American robotics industry sales have exploded with a 63.6% increase in a single quarter of 2019. The pandemic has accelerated this growth rate dramatically. RIA statistics show that North American companies ordered 31,044 robotic units, valued at roughly $1.6 billion in 2020.
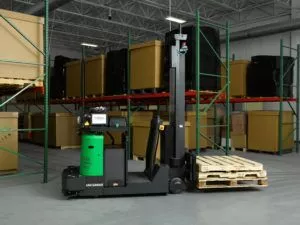
The trend to adopt warehouse automation is catching on with the recognition that there is a huge opportunity for improved productivity and labor efficiency. However, implementing modern technology in legacy systems can be a challenge. Flexible systems are key to seamless integration. AMR solutions paired with orchestration technology enable more flexible and resilient operations as demands fluctuate day-to-day and season-to-season. The roles of automated material handling robots are expanding and facilities are now relying on their support to meet their demands.
To learn more about how AMRs mitigate the cost of transporting non-conveyables, as well as additional benefits of material handling automation, read more in Inbound Logistics.