Milk runs in logistics refers to a type of delivery method in which a single vehicle makes multiple stops at different locations to pick up or drop off goods. The term “milk run” in logistics comes from the practice of milkmen in the dairy industry delivering milk door-to-door in the early 20th century.
Where do milk runs take place?
This type of delivery system is used in many industries, including manufacturing, retail, and healthcare. In manufacturing, for example, a milk run can be used to deliver raw materials to different factories within a company’s supply chain. In retail, a milk run can be used to deliver products from a distribution center to multiple stores. In healthcare, a milk run can be used to deliver medical supplies to different hospitals or clinics.
Benefits of milk runs
The main benefit of a milk run is that it allows for an efficient use of resources. By making multiple stops at different locations, a milk run can save on transportation costs and reduce the number of vehicles needed to make deliveries. This can also help to reduce congestion on the roads and decrease the environmental impact of transportation.
Another benefit of a milk run is that it allows for greater flexibility in scheduling deliveries. Because a single vehicle makes multiple stops, it can be scheduled to make deliveries at different times of the day or week, depending on the needs of the business. This can help to reduce delays and idle time and improve the overall efficiency of the delivery system.
Challenges with milk runs
However, there are also some challenges associated with milk runs. One of the biggest challenges is coordinating the delivery schedule so that all stops are made in the most efficient order. This can be difficult to manage, especially when dealing with a large number of stops and a complex delivery schedule.
Another challenge is ensuring that the right goods are delivered to the right locations. This can be difficult to manage, especially when dealing with a large number of stops and a complex delivery schedule.
In order to overcome these challenges, businesses often use advanced logistics software and GPS tracking systems to manage milk runs. These tools can help optimize the delivery schedule and ensure the right goods are delivered to the right locations.
Types of common milk runs
Milk runs come in different types, each with its own advantages and disadvantages.
- The closed loop milk run follows a fixed schedule to deliver to a set of locations, making it efficient but less flexible.
- The open loop milk run delivers to variable locations as needed, offering more flexibility but can be challenging to manage.
- A hybrid of the two is the milk run with cross-docking, which is based on a closed loop but allows for some stops to be added or removed as needed, providing both efficiency and flexibility.
Milk runs logistics refer to the practice of making multiple pickups and deliveries at different locations in a single trip. This method is often used in the transportation of goods and materials and can be done using various types of robots.
How is automation used to make milk runs more efficient?
One common type of robot used in milk runs logistics is the autonomous mobile robot (AMR). These robots are equipped with sensors and navigation systems that allow them to move around a facility and pick up and deliver items without human intervention. They can be programmed to follow specific routes and can be integrated with warehouse management systems for real-time tracking and monitoring.
Another type of robot used in milk runs logistics is the autonomous guided vehicle (AGV). These robots are similar to AMRs in that they are capable of moving around a facility and transporting goods, but they are typically larger in size and can carry heavier loads. AGVs typically navigate using sensors that are programmed to follow specific routes, which is also a limitation of this legacy technology.
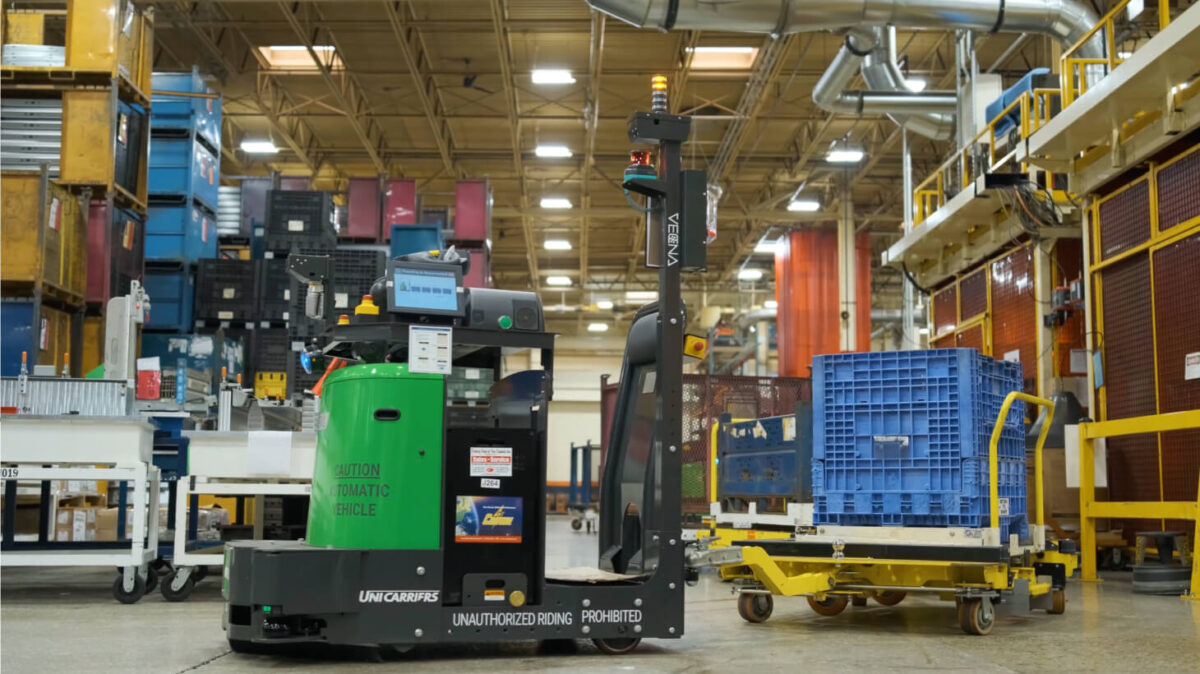
Overall, milk runs in logistics are used to drive resource efficiency, offer greater flexibility in scheduling deliveries, reduce congestion on the roads and decrease the environmental impact of transportation. However, it also comes with challenges such as coordinating the delivery schedule and ensuring the right goods are delivered to the right locations. Overall, the use of robots in milk runs can help improve efficiency, reduce costs, and increase safety. By automating repetitive tasks, robots can free up human workers to focus on more complex and value-added activities. Additionally, with the use of sensors and navigation systems, robots can ensure that deliveries are made on time and with minimal errors and can also aid in the tracking and monitoring of goods in real-time.
Automation solutions for milk runs
Vecna Robotics has a wide range of solutions that are tailor-made for automating milk runs in logistics. For more information about how you can get started with your finished goods automation journey, go to our From No Bot to Robot page, or can contact us today to schedule a consultation with a factory automation expert.