Robotic case palletizing in warehouses and manufacturing facilities are increasingly using Automated mobile robots (AMRs) in the palletizing process. Palletizing involves stacking boxes or other items onto a pallet in a specific pattern or configuration. This task is often done manually, but AMRs can significantly speed up the process and reduce the need for human labor.
AMRs are equipped with sensors and software that allow them to navigate through a warehouse or facility, locate items to be palletized, and deliver them to a manual or robotic palletizing station. Once palletized, they can also deliver completed pallets to stretch wrappers and the outbound shipping dock. They can also communicate with other systems, such as warehouse management systems, to ensure that the correct orders are prioritized and the correct inventory is replenished.
Benefits of using AMRs for case palletizing
One of the key benefits of using AMRs for palletizing is increased efficiency. These robots can work 24/7 and do not need breaks or time off, which means that they can keep pace with high-volume production and help to minimize downtime. Additionally, AMRs can be programmed to optimize the palletizing process, for example, by sequencing deliveries to optimize the efficiency of robotic palletizers and reduce downtime.
AMRs can also improve safety in the workplace. By taking over the task of transporting mixed-case and empty pallet stacks, they can reduce the likelihood of unstable loads causing an accident. They can also improve the accuracy of the palletizing process, which can help to reduce the likelihood of errors that could lead to product damage or loss.
Another advantage of using AMRs for palletizing is flexibility. These robots can be reprogrammed to handle different types of pallet configurations and can be easily moved to different areas of a facility as needed. This allows companies to quickly adapt to changing production needs or order profiles.
Challenges of robotic case palletizing with AMRs
However, there are also some challenges associated with using AMRs for palletizing. One of the main challenges is the cost of the technology. AMRs can be expensive to purchase and maintain, particularly if you purchase the equipment up-front as a capital expense. Fortunately, some vendors offer flexible financing programs like Vecna’s Robots as a Service, that roll up all costs related to your automation program into a single, low annual payment. Additionally, AMRs require skilled personnel to operate and maintain them, which can also add to the cost. But remote monitoring and big advances in autonomous navigation have allowed these systems to deliver upwards of 99.9% uptime.
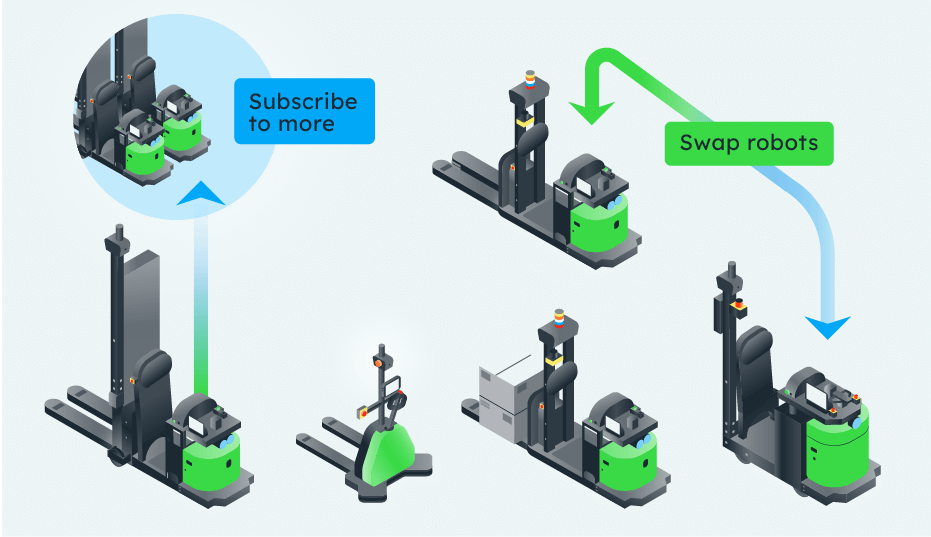
Another challenge is the integration of AMRs with existing systems and equipment. These robots need to be able to communicate with other systems in the facility, such as warehouse management systems, in order to function effectively. This can require significant investment in software and hardware and may require the involvement of specialized IT personnel. Access to secure, high-speed wireless in large warehouse facilities is typically another challenge that some operations run into when they are looking to deploy modern robotics.
Finally, there is the issue of regular maintenance and reliability. AMRs are complex machines and when they stop can disrupt production and cause delays, which can be costly for businesses. Therefore, companies need to be prepared to invest in regular maintenance and repairs to ensure that the AMRs are operating at optimal performance. However, programs like Vecna Robotics’ Robots as a Service already include remote monitoring, maintenance and in-field services to help minimize downtime and unexpected maintenance costs.
The case for AMRs in palletizing
AMRs offer significant benefits for the palletizing process in warehouses and manufacturing facilities. They can increase efficiency, improve safety, and provide flexibility in the production process. However, there are also challenges associated with using different types of AMRs, such as cost, integration and reliability. When determining your alternatives for automating case palletizing you need to weigh the benefits and challenges carefully of each AMR solution and consider the full automation journey beyond the near-term cost/benefits.
Vecna’s solution
Vecna Robotics has a wide range of pallet handling solutions that can help you automate case palletizing in your facility. For more information about how you can get started with your finished goods automation journey, go to our From No-bot to Robot page. If you would like to evaluate the full cost of an automation solution for case palletizing, consult our Return on Robotics Calculator or you can contact us today to schedule a consultation with a factory automation expert.