A guide to Material Handling Equipment and the 5 Technologies Shaping Warehouses, Distribution Centers, and Production
Our bustling modern economy relies on the movement of materials, making material handling equipment (MHE) an integral part of our day-to-day lives – whether we realize it or not. From manufacturing to warehousing, to distribution, almost every major industry relies on efficient material handling equipment. So how can we make sure we’re getting MHE right? This comprehensive guide will provide an in-depth look at the diverse types of material handling equipment that facilitate the seamless movement and storage of goods.
From manual tools to advanced automated systems, we’ll explore how these technologies support everyday operations and drive innovations across industries, and dive into the transformative effects of emerging material handling automations, that are reshaping the landscape and the future. Join us on this detailed journey to understand the critical tools and technologies that are setting new standards in industrial efficiency and operational excellence.
4 Types of Material Handling Equipment
Material handling equipment is classified into several categories, each serving a specific function in the movement, storage, control, and protection of materials and products. These categories include storage equipment, engineered systems, industrial trucks, and bulk material handling equipment.
1. Storage Equipment
Storage equipment is designed to hold products or materials in a facility. While this equipment primarily focuses on long-term storage, it also plays a crucial role in efficient material handling by facilitating easy access and movement when needed.
- Pallet Racks: Pallet racks are one of the most common forms of storage in warehouses. They are designed to hold pallets of goods in a stacked formation, maximizing vertical space. Pallet racking systems come in various forms, including selective racks, drive-in/drive-thru racks, push-back racks, and pallet flow racks. Selective racks allow for easy access to each pallet, making them suitable for facilities where inventory turnover is high.
- Cantilever Racks: Cantilever racks are ideal for storing long, bulky items like pipes, lumber, or steel bars. These racks consist of vertical columns with arms extending out, providing support for the stored materials. The open design allows for easy loading and unloading using forklifts or by hand.
- Mezzanines: Mezzanines are elevated platforms within a warehouse or distribution center, used to create additional floor space for storage or operations. They are customizable and can be integrated with conveyors, lifts, or other material handling systems.
- Shelving Units: These are smaller storage units typically used for lighter items. They are commonly found in smaller warehouses, parts distribution centers, and manufacturing facilities. Shelving units can range from simple, adjustable shelving to more complex systems with integrated bin storage.
- Bins and Totes: Bins and totes are used for storing small parts, components, or materials. They are often integrated with shelving units or conveyors and are essential in industries like automotive, electronics, and assembly operations where small parts need to be organized and easily accessible.
2. Engineered Systems
Engineered systems are automated or semi-automated systems designed to move and store materials. They are often integrated with other material handling equipment to create a cohesive, efficient system.
- Conveyor Systems: Conveyors are used to move materials from one location to another within a facility. They come in various forms, including belt conveyors, roller conveyors, and overhead conveyors. Belt conveyors are typically used for moving products over long distances, while roller conveyors are suitable for transporting items that require smooth movement. Overhead conveyors are ideal for moving items over obstructions or between different levels in a facility.
- Automated Storage and Retrieval Systems (AS/RS): AS/RS are highly automated systems that store and retrieve materials as needed. These systems typically consist of storage racks, automated cranes or shuttles, and control software. AS/RS is particularly useful in high-density storage environments, where space is at a premium and manual retrieval would be inefficient or impossible.
- Robotic Systems: Robotic systems are increasingly used in material handling for tasks such as picking, packing, and palletizing. These systems can be programmed to handle a wide range of materials and products, making them versatile and highly efficient. Robotic arms, for example, are used in manufacturing to assemble products, while autonomous mobile robots (AMRs) can navigate warehouses to transport goods from one location to another.
- Automated Guided Vehicles (AGVs): AGVs are mobile robots that follow predetermined paths to transport materials within a facility. They are commonly used in large warehouses and manufacturing plants where materials need to be moved over long distances. AGVs can be programmed to follow specific routes, making them ideal for repetitive tasks like transporting goods between different stages of production.
3. Industrial Trucks
Industrial trucks are vehicles used to transport materials within a facility. They are versatile and can handle a wide range of tasks, from moving heavy pallets to transporting smaller items.
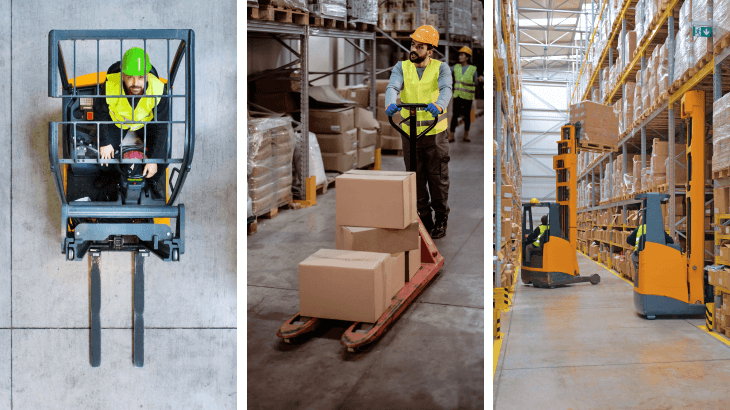
- Forklifts: Forklifts are perhaps the most iconic piece of material handling equipment. These powered trucks come in various configurations, including counterbalance, reach, and side loader forklifts. They are essential for lifting and transporting heavy loads, particularly in environments where pallets are used extensively.
- Pallet Jacks: Pallet jacks are a more manual alternative to forklifts, used primarily for lifting and moving pallets over short distances. While they require manual operation, electric pallet jacks offer powered movement and lifting capabilities, making them suitable for heavier loads.
- Order Pickers: Order pickers are specialized forklifts designed for picking individual items from high shelving units. They are commonly used in distribution centers and warehouses where individual orders are picked and packed for shipping.
- Hand Trucks: Hand trucks, or dolly carts, are manually operated trucks used for moving smaller loads. They are commonly used in smaller warehouses, retail stores, and offices for moving boxes, packages, and other manageable items.
- Tow Tractors: Tow tractors are used to pull trailers or carts loaded with materials. They are particularly useful in large warehouses or manufacturing plants where materials need to be transported over long distances.
4. Bulk Material Handling Equipment
Bulk material handling equipment is used to move and store large quantities of materials, typically in loose form. This type of equipment is essential in industries like mining, agriculture, and construction.
- Conveyors for Bulk Materials: These conveyors are specifically designed to move loose materials like grains, coal, or ores. Belt conveyors, screw conveyors, and bucket elevators are common examples. Each type of conveyor is designed to handle specific types of materials, ensuring efficient transport and minimal spillage.
- Stackers and Reclaimers: Stackers are used to pile bulk materials in large storage areas, while reclaimers are used to retrieve these materials for further processing. These machines are commonly used in industries like mining, where large quantities of material need to be stored and retrieved efficiently.
- Hoppers and Silos: Hoppers and silos are used for storing bulk materials. Hoppers are often used as temporary storage units before materials are processed or transported, while silos provide longer-term storage. Both are crucial in industries like agriculture and manufacturing, where materials like grain, cement, or chemicals need to be stored in large quantities.
- Dust Collectors: Dust collectors are used to capture and remove dust particles generated during the handling of bulk materials. They are essential in industries where dust can pose a health hazard or impact product quality, such as in grain processing or cement manufacturing.
5 Automation technologies advancing Material Handling Equipment
Automation is revolutionizing the field of material handling, driving efficiency, reducing labor costs, and minimizing errors. As companies look to optimize their operations, the adoption of automated material handling systems is accelerating. This section will explore the various types of material handling automation, the workflows they automate, and the top vendors in each category.
1. Automated Storage and Retrieval Systems (AS/RS)
AS/RS systems are designed to store and retrieve materials automatically, without the need for human intervention. These systems are typically used in high-density storage environments where space is limited, and efficiency is critical.
- How They Work: AS/RS systems use cranes or shuttles that move along tracks to retrieve or store items in racks. These systems are controlled by software that manages inventory and ensures that the correct items are retrieved or stored. The system can operate 24/7, increasing throughput and reducing the need for manual labor.
- Workflows Automated: AS/RS systems automate the storage and retrieval of materials, particularly in environments where items need to be retrieved frequently or where space is at a premium. They are commonly used in warehouses, distribution centers, and manufacturing facilities.
- Top Vendors:
- Dematic: Known for its advanced AS/RS solutions that integrate seamlessly with other material handling systems.
- Swisslog: Offers a wide range of AS/RS solutions, including robotic and shuttle systems.
- Honeywell Intelligrated: Provides scalable AS/RS systems tailored to the needs of various industries.
2. Automated Guided Vehicles (AGVs) and Autonomous Mobile Robots (AMRs)
AGVs and AMRs are mobile robots used to transport materials within a facility. While AGVs follow predetermined paths, AMRs are more flexible and can navigate dynamic environments.
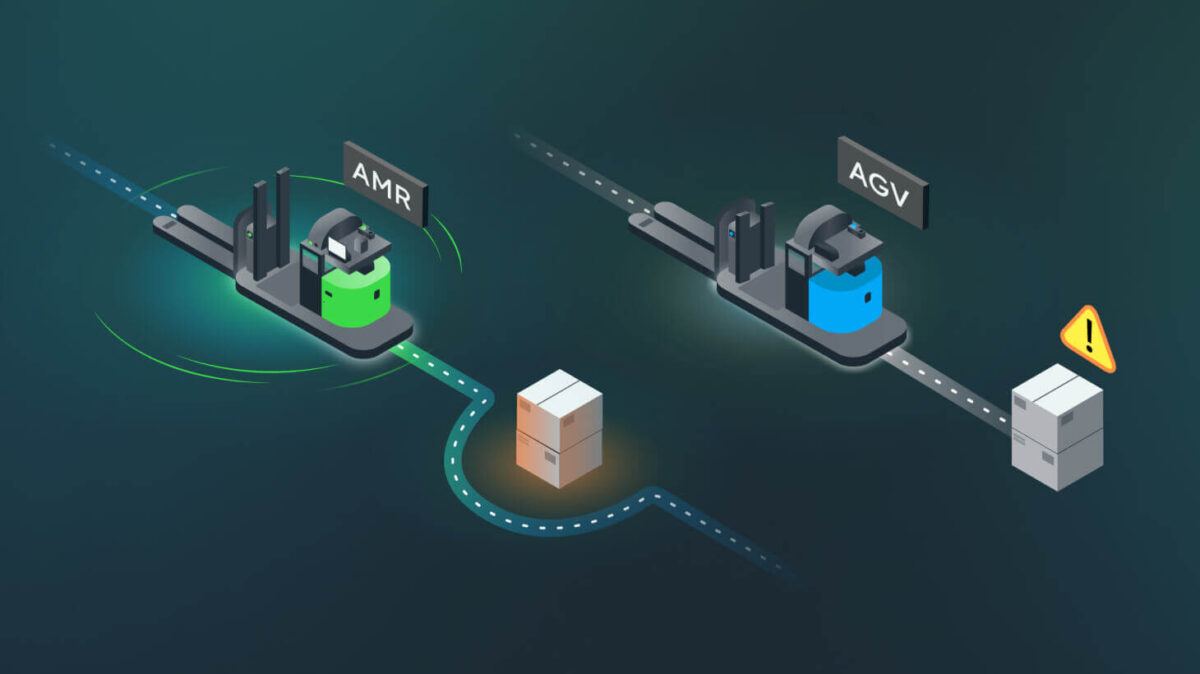
- How They Work: AGVs follow magnetic strips, wires, or other predefined paths, while AMRs use advanced sensors and AI to navigate through a facility autonomously. Both types of robots are used to transport materials, reducing the need for human-operated forklifts or pallet jacks.
- Workflows Automated: AGVs and AMRs automate the transportation of materials within a facility, whether it’s moving goods from a production line to storage or delivering items to shipping areas. They are particularly useful in large warehouses and manufacturing plants where materials need to be moved over long distances.
- Top automated material handling equipment suppliers:
- KION Group (Linde, STILL): Offers a variety of AGVs and AMRs for different industrial applications.
- Oceaneering International: Known for its robust AGVs used in heavy industrial applications.
- Fetch Robotics: Specializes in AMRs that can integrate with existing warehouse management systems.
- Vecna Robotics: Is known as the industry leader in ground-to-ground and low-lift flexible AMR systems and innovative robots as a service program.
3. Robotic Picking and Packing Systems
Robotic picking and packing systems use robots to select items from shelves and pack them into boxes for shipping. These systems are becoming increasingly popular in e-commerce and distribution centers.
- How They Work: These systems use robotic arms or mobile robots equipped with sensors and AI to identify, pick, and pack items. The robots are integrated with inventory management systems, ensuring that the correct items are selected and packed.
- Workflows Automated: Picking and packing systems automate the order fulfillment process, reducing the need for manual labor and increasing the speed and accuracy of order processing. They are particularly valuable in high-volume e-commerce operations where speed is critical.
- Top automated material handling equipment suppliers:
- ABB: Offers advanced robotic picking systems used in various industries.
- Fanuc: Known for its versatile robotic arms that can be used for picking, packing, and palletizing.
- RightHand Robotics: Specializes in AI-powered robotic picking systems designed for e-commerce and retail distribution centers.
4. Conveyor Systems with Integrated Automation
While conveyors have been a staple in material handling for decades, the integration of automation has significantly enhanced their capabilities. Modern conveyor systems can be equipped with sensors, sorters, and automated controls to streamline the movement of goods.
- How They Work: Automated conveyors use sensors to detect the presence of materials and sort them as needed. The system can be programmed to direct items to different destinations based on criteria such as size, weight, or destination.
- Workflows Automated: Automated conveyor systems are used to move and sort materials within a facility, reducing the need for manual sorting and transport. They are particularly useful in distribution centers where items need to be sorted and directed to different shipping lanes.
- Top Automated material handling equipment suppliers:
- Daifuku: Offers advanced conveyor systems with integrated sorting and control capabilities.
- TGW Logistics Group: Known for its high-speed conveyor systems used in e-commerce and retail distribution.
- Murata Machinery: Provides automated conveyor systems with advanced sorting and tracking features.
5. Warehouse Management Systems (WMS) with Integrated Automation
Warehouse Management Systems (WMS) are software platforms that manage inventory, track orders, and optimize warehouse operations. When integrated with automated material handling equipment, WMS can significantly enhance efficiency and accuracy.
- How They Work: WMS integrates with various automated systems, including AS/RS, AGVs, and robotic picking systems. The WMS manages inventory, tracks orders, and directs automated systems to perform specific tasks, such as retrieving items for an order or directing an AGV to transport goods.
- Workflows Automated: WMS automates the management of inventory, order fulfillment, and warehouse operations. By integrating with automated systems, WMS can optimize the flow of materials within a facility, reducing bottlenecks and ensuring that orders are processed accurately and efficiently.
- Top automated material handling equipment suppliers:
- Manhattan Associates: Provides a comprehensive WMS with advanced automation integration.
- SAP: Known for its robust WMS that can integrate with various automated systems.
- Oracle: Offers a cloud-based WMS with extensive automation capabilities.
The Future of Material Handling: A Look Ahead
As automation continues to advance, the future of material handling will likely be defined by greater efficiency, flexibility, and integration. Here are some key trends that are expected to shape the future of material handling:
1. Increased Adoption of AI and Machine Learning
Artificial intelligence (AI) and machine learning (ML) are expected to play a crucial role in the future of material handling. These technologies can be used to optimize workflows, predict maintenance needs, and enhance the capabilities of automated systems. For example, AI-powered robots can learn from their environment and improve their picking accuracy over time, while ML algorithms can optimize inventory management and reduce the risk of stockouts.
2. Expansion of Autonomous Systems
The use of autonomous systems, such as AMRs and drones, is expected to expand significantly. These systems will become more capable and versatile, able to navigate complex environments and handle a wider range of tasks. In the future, it’s possible that entire warehouses could be operated with minimal human intervention, with autonomous systems handling everything from receiving and storing goods to picking and shipping orders.
3. Integration of IoT and Smart Sensors
The Internet of Things (IoT) and smart sensors will play a key role in the future of material handling. These technologies can provide real-time data on the status of equipment, the location of goods, and the efficiency of workflows. By integrating IoT and smart sensors with automated systems, companies can gain greater visibility into their operations and make data-driven decisions to improve efficiency and reduce costs.
4. Development of Flexible and Modular Systems
As the needs of businesses continue to evolve, there will be a growing demand for flexible and modular material handling systems. These systems can be easily reconfigured or expanded to accommodate changes in product lines, order volumes, or facility layouts. This flexibility will be particularly valuable in industries like e-commerce, where demand can fluctuate rapidly.
5. Focus on Sustainability
Sustainability will become an increasingly important consideration in material handling. Companies will seek out automated systems that are energy-efficient, produce less waste, and have a smaller environmental footprint. For example, AGVs and AMRs powered by renewable energy sources could become more common, and the use of recyclable or biodegradable materials in packaging and storage will likely increase.
Material handling equipment is essential for the smooth operation of warehouses, distribution centers, and factories. As automation continues to evolve, it is reshaping the landscape of material handling, driving efficiency, reducing costs, and minimizing errors. The rise of automated systems like AS/RS, AMRs, robotic picking systems, and WMS is transforming the way materials are stored, moved, and managed. Looking ahead, the integration of AI, autonomous systems, IoT, and sustainable practices will further enhance the capabilities of material handling systems, making them more efficient, flexible, and environmentally friendly. As companies continue to adopt and innovate in this space, the future of material handling promises to be both exciting and transformative.