The past year has brought many challenges for logistics-based companies. Faced with rapidly-shifting economic conditions, unpredictable consumer behaviors, an ongoing labor shortage and an increasingly competitive landscape, those in material handling have been forced to adapt quickly or fall behind. These drastic changes have supply chain managers looking toward scalable, flexible solutions that will increase their operation’s preparedness for future disruption. The first step in achieving this is integrating robotic material handling. Read on if you’re wondering: how do I know it’s time to automate logistics, and where do I start?
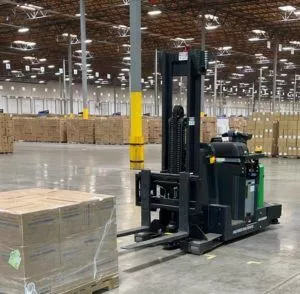
1. When a worker’s job is dangerous, repetitive, or hard to fill
As shipment rates increase, many jobs in material handling are becoming increasingly strained. Many jobs have shifted to consisting of nearly entirely repetitive tasks, leaving workers unsatisfied and less productive. This does very little to alleviate dangers associated with these jobs, as accident rates involving manually-operated vehicles continue to rise. These two factors have led to high turnover rates and an unsustainable labor gap that plagues the material handling industry, costing millions in lost productivity each year.
Logistics automation solves this by allowing robots to take over the dull and dangerous tasks that workers don’t want to do. This allows workers to be moved to high-value tasks that humans are more suited for, increasing employee safety and satisfaction.
2. When labor scheduling for flexible demand is not working
With the ongoing labor shortage, labor scheduling has become a precarious balancing act. Beyond this, flexible demand planning is becoming more and more difficult as consumer demands shift drastically without warning. Mistakes in this area are costly, and not being able to meet market expectations can cause firms to lose market share or goodwill in partnerships.
The pressures of inaccurate scheduling are alleviated with robots, as they are available to turn on or go offline at a moment’s notice. When facing extreme spikes in seasonal demand, robots can work around the clock to meet production or order fulfillment goals. Automated Mobile Robot (AMR) solutions like Vecna Robotics’ are scalable and increase adaptability through flexible automation. Programs like Robot-as-a-Service allow for facilities to “rent” robots, adding or removing units as needed.
3. When order fulfillment or per square foot costs are high
Automation helps lower costs and increase profits by boosting productivity. Robots are able to work around the clock, making operations more efficient. Vecna Robotics’ AMRs are enabled with the ability to plot potential routes and choose the best option based on factors like distance, traffic, and location of the stops along the route. This level of intelligence means optimized movements and increased efficiency.
With Vecna Robotics’ workflow orchestration software, Pivotal, cycle time can be reduced and throughput doubled with optimized movements. Pivotal works similarly to a warehouse management system but uses advanced algorithms to balance demand and dynamically assign tasks to both humans and robots.
4. When you’re handling more SKUs or non-conveyable shipments
A surge in e-commerce has led to an extreme level of SKU-proliferation and non-conveyable orders. This trend has caused inventory costs to balloon and margins to plummet. Maintaining a high-SKU inventory is expensive, and non-conveyable shipments can interrupt logistics workflows and cause bottlenecks. Before this shift, companies could temporarily solve these problems by throwing more people into the mix. As the labor gap continues and these conditions persist, this solution becomes less and less practical.
Integrating automated logistics solutions allows for workers to be allocated to trickier logistics tasks as needed. AMRs turn troublesome non-conveyable loads into efficient transports, eliminating repetitive, manual operations while offering flexibility in what’s moved and when. They also offer increased inventory accuracy, which can reduce the stress of distributing and packaging many SKUs.
5. When you want to stay ahead of the competition
Automation provides many advantages, including increased efficiency and adaptability that can be vital in today’s shifting market. The implementation of AMRs can counter big competitors that push industry margins down. Vecna Robotics’ vehicles are ever-improving, meaning the advantage they provide stays competitive.
Anyone can automate. With scalable, interoperable, and infrastructure-free self-driving materials handling equipment, facilities can automate logistics workflows at any point in operations.
Learn more about how to automate logistics workflows.